Сварка Банников Евгений
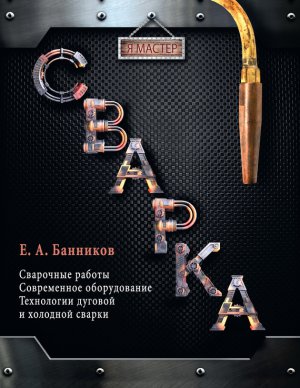
Введение
Сварка – это технологический процесс получения неразъемных соединений посредством установления межатомных связей между свариваемыми частями при их нагревании или пластическом деформировании, или совместном действии того и другого.
Благодаря своей относительной простоте применения, быстроте соединения различных материалов сварка находит широкое применение.
Сварка является экономически выгодным, высокопроизводительным технологическим процессом, что обеспечивает ее использование во всех областях машиностроения, строительства, науки и техники. Например, при замене клепаных конструкций на сварные соединения экономия металлов составляет 15–20 %, а при замене литых деталей сварными – около 50 %. Сварка является необходимым технологическим процессом обработки металлов. В настоящее время сваркой соединяют разнородные и однородные материалы: металлы и неметаллы – от нескольких микрон в микросхемах до нескольких метров – в тяжелом машиностроении. Трудно назвать отрасль промышленности, которая обходилась бы без применения сварки. Сваркой соединяют детали космических кораблей, лопасти турбин, корпуса подводных лодок и самолетов, корпуса приборов и выводы микросхем. Детали, соединенные сваркой, имеют прочность, равную прочности основного металла.
Различают два вида (способа) сварки по типу энергетического воздействия:
• сварка плавлением (с применением тепловой энергии);
• сварка давлением (с применением механической энергии).
В первом случае материал в месте соединения расплавляют, а во втором процесс выполняют с приложением давления и местным нагревом или без него.
Энергия в зону сварки вводится в виде теплоты, упругопластической деформации, электронного, ионного, электромагнитного и других видов воздействия.
В зависимости от формы энергии, используемой для образования сварного соединения, все виды сварки разделяют на три класса:
• К термическому классу (Т) относятся виды сварки, осуществляемой плавлением с использованием тепловой энергии. Основными источниками теплоты являются сварочная дуга, плазма, лучевые источники энергии (лазерное, электронное, фотонное излучение), теплота, выделяемая при химических реакциях (газовая, термитная).
• К механическому классу (М) относятся виды сварки, осуществляемые с использованием механической энергии и давления (ультразвуковая, взрывом, трением).
• К термомеханическому классу (ТМ) относятся виды сварки с использованием тепловой энергии и давления (диффузная сварка, контактная и др.).
Наибольший объем среди всего разнообразия видов сварки занимает дуговая сварка, в частности ручная дуговая электросварка. Источником теплоты при этом является электрическая дуга, которая горит между электродом и заготовкой.
Впервые мысль о возможности практического использования «электрических искр» для плавления металлов высказал в 1753 г. академик Российской Академии наук Г. Р. Рихман, исследовавший атмосферное электричество.
В 1802 г. профессор Санкт-Петербургской военно-хирургической академии Василий Владимирович Петров открыл явление электрической дуги. Петров исследовал возможности использования электричества для освещения. Им был собран «Вольтов столб» из 2 400 пар медно-цинковых кружков, с проложенной между ними бумагой, смоченных раствором нашатыря. Это была одна из самых мощных электрических батарей того времени.
В. В. Петров в своих трудах первым описал явление электрической дуги и показал возможность использования теплоты, выделяемой дугой, для плавления металлов.
Этим открытием, одним из самых значительных в XIX веке, В. В. Петров положил начало развитию новых технических знаний и науки, получивших дальнейшее практическое применение в электродуговом освещении, электрическом нагреве, плавке и сварке металлов.
Однако в то время это открытие не нашло практического применения. Спустя почти 80 лет наш русский изобретатель Н. Н. Бенардос в 1892 г. начал разработку практического применения электрической дуги для сварки металлов. Н. Н. Бенардос в 1885–1887 гг. запатентовал свой способ сварки «Электрогефест», или «Способ соединения и разъединения металлов непосредственным действием электрического тока», в 13 странах, в том числе и в Америке, хотя американский ученый И. Томпсон в 1867 г. одним из первых в мире пытался сварить два куска металла электросваркой.
В 1892 г. на электротехнической выставке, проходившей в Петербурге, Н. Н. Бенардос представил описание своего изобретения: «Электропайка, электросварка, электроотливка, электронаслоение, электросверление, электроразрезывание всех металлов». Он присоединял один полюс динамо-машины к листу металла, а другой к угольному электроду. В пламя дуги вводили металлический стержень.
Но Бенардос не догадался о том, что можно не вводить посторонний металл при плавящемся электроде. Это сделал русский ученый Н. Г. Славянов. Его «Способ электрической отливки металлов» увидел весь мир. На выставке в 1893 г. Славянов получил золотую медаль «За дуговую электросварку». Он представил двенадцатигранную призму из никеля, томпака, стали, чугуна, нейзильбера, бронзы обычной и колокольной, где все грани были соединены сваркой. После этого Америка уже не сомневалась в возможностях сварки цветных металлов по способу Н. Г. Славянова.
С именами Н. Г. Славянова и Н. Н. Бенардоса связано развитие металлургических основ электрической дуговой сварки, контактной сварки, создание первого автоматического регулятора длины дуги и первого сварочного генератора. Н. Г. Славяновым были предложены флюсы для получения высококачественного металла сварных швов. В Московском политехническом музее демонстрируется подлинный сварочный генератор Н. Г. Славянова и образцы сварных соединений.
В начале 1930-х годов в связи с потребностью в более прогрессивных способах соединения металлов стала развиваться сварочная техника. В 1929 г. советский инженер-изобретатель Д. А. Дульчевский разработал способ автоматической дуговой сварки под флюсом. Под руководством академика В. П. Вологдина в 1924–1935 гг. с использованием электрической дуговой сварки были изготовлены первые отечественные котлы и корпуса судов. Сварку применяли ручную дуговую, электродами с тонкими ионизирующими покрытиями.
В 1935–1939 гг. стали применять легированные электроды с толстым покрытием. Их применение позволило использовать сварку в изготовлении промышленного оборудования и строительных конструкций.
Огромный вклад в развитие сварочных технологий внес киевский институт им. Е. О. Патона.
Здесь была разработана электрошлаковая сварка, изготовлены высокоскоростные сварочные машины для сварки под флюсом. Применение электрошлаковой сварки позволило заменить литые и кованые крупногабаритные изделия сварными, более технологичными.
В период Великой Отечественной войны сварка получила широкое применение в военной технике, были разработаны уникальные способы сварки броневых сталей. В послевоенное время при восстановлении народного хозяйства сварка как прогрессивный способ соединения металлов значительно вытеснила клепку.
С 1948 г. промышленное применение получили новые способы сварки: сварка в среде защитных газов, ручная, механизированная и автоматическая сварка плавящимся и неплавящимся электродом.
В 1950–1952 гг. в ЦНИИТмаше при участии МВТУ им. Н. Э. Баумана и ИЭС им. Е. О. Патона под руководством профессора К. Ф. Любавского была разработана сварка низколегированных и низкоуглеродистых сталей в среде углекислого газа. Сейчас этот способ сварки составляет 30 % объема всех сварочных работ.
В конце 1950-х годов французскими учеными был разработан новый вид сварки плавлением – электронно-лучевой, получивший широкое применение в производстве микроэлектронной техники и выплавке особо чистых сплавов.
Впервые в мире советские космонавты В. Кубасов и Г. Шонин в 1969 г. осуществили автоматическую сварку и резку металлов в открытом космосе. В 1984 г. космонавты С. Савицкая и В. Джанибеков провели ручную сварку, резку и пайку различных металлов в космосе. В настоящее время сварку и резку металлов проводят в космосе, под водой, в вакууме и на открытом воздухе.
Открытая и разработанная Н. Н. Бенардосом в 1887 г. контактная и шовная сварка широко применяется в настоящее время. Кузов современного автомобиля, состоящий из тонколистовых штампованных деталей, сварен более чем в 10 тысячах точек. Самолет насчитывает уже несколько миллионов сварных точек или «электрозаклепок».
Наряду с дуговой электросваркой, к сварке плавлением относят газовую сварку. Для плавления металлов используют тепло пламени смеси газов, сжигаемых с помощью горелки. Газовая сварка классифицируется по виду применяемого горючего газа: ацетиленокислородная, керосино-кислородная, бензино-кислородная, пропанобутано-кислородная, водород-кислородная и др.
Способ газовой сварки был разработан в конце XIX столетия, когда началось промышленное производство кислорода, водорода и ацетилена. В этот период газовая сварка являлась основным способом сварки металлов и обеспечивала получение наиболее прочных соединений. Наибольшее развитие газовая сварка с применением ацетилена получила в период развития сети железных дорог и вагоностроения. Необходимо было производить большой объем работ по сборке вагонов, паровозов. В настоящее время газовая сварка применяется во многих отраслях промышленности: при изготовлении и ремонте изделий из тонколистовой стали, сварке цветных металлов и их сплавов, а также при наплавочных работах. Разновидностью газопламенной обработки является газотермическая резка, широко применяемая на этапе заготовительных операций при раскрое металлов и резке металлолома.
Несмотря на многочисленные способы применения механизированных и автоматизированных видов сварки, масштабы применения ручной дуговой электросварки увеличиваются. Это связано с созданием новых материалов и оборудования для производственных процессов. На эти позиции ручную сварку выдвинули высокая скорость соединений металлов и технологичность процесса.
Начальной и конечной операцией создания современных конструкций часто является ручная дуговая сварка.
Глава 1
Термический класс сварки
Классификация видов сварки плавлением
Термический класс сварки включает все виды сварки с использованием тепловой энергии.
Сварку плавлением в зависимости от различных способов, характера источников нагрева и расплавления свариваемых кромок деталей можно разделить на следующие основные виды:
• газовая сварка;
• электрическая дуговая сварка;
• электрошлаковая сварка;
• электронно-лучевая сварка;
• плазменная сварка;
• лазерная сварка;
• термитная сварка.
Этот класс характеризуется тем, что сварка осуществляется плавлением кромок соединяемых частей. При этом образуется ванна расплавленного металла. После отвода источника нагрева металл сварочной ванны кристаллизуется и образуется сварной шов, соединяющий свариваемые части. Сварка – сложный и быстропротекающий физико-химический процесс образования соединения материалов. Подготовка заготовок и продуманная технология делают сварку легкой, быстрой.
Из курса физики нам известно, что состояние любого вещества характеризуется взаимосвязью молекул и атомов. Различают четыре основные состояния материи:
• твердое;
• жидкое;
• газообразное;
• плазму.
Твердое тело представляет собой «агрегат» атомов, находящихся во взаимодействии, а его физические характеристики определяются их взаимным расположением (кристаллической решеткой) и химическими связями, действующими между ними.
Соединение сваркой твердых тел можно представить как образование прочных и устойчивых химических связей между атомами соединяемых элементов. Для получения прочного соединения твердых тел необходимо их сблизить до возникновения межатомных связей.
В твердом и жидком состоянии расстояние между молекулами и атомами очень мало. Этим объясняется малая сжимаемость этих веществ и их общее название – «конденсированное состояние».
В газах расстояние между молекулами значительно больше, поэтому газы сравнительно легко сжимать под воздействием внешнего давления.
Различие в электропроводности твердых, жидких и газообразных веществ также объясняется различием расстояний между атомами и молекулами. В твердых и жидких веществах крайние электроны, далеко отстоящие от ядер своих атомов, легко теряют связь с ядром. Благодаря этому появляются свободные электроны, легко перемещающиеся по объему вещества. Такие свободные электроны называются электронами проводимости и являются носителями тока в проводниках. В газах электроны притягиваются только к своим ядрам, поэтому при нормальных условиях газы электрический ток не проводят.
Вся история человечества связана с освоением энергии, в частности тепловой энергии. От древнего пламени костра до управления потоками света в лазерном луче – вот история технологии. В таблице 1 приведены данные о плотности потоков тепловой энергии и минимально достижимых площадях нагрева материалов, т. е. фокусировке потоков энергии в пятно нагрева.
Таблица 1
Энергетические свойства источников тепла
Классификацию сварки можно провести по степени механизации процессов. Тогда выделяют сварку: ручную, механизированную (полуавтоматическую), автоматическую.
Ручная сварка производится оператором (сварщиком) с помощью инструмента вручную, без применения механизмов.
Механизированная сварка выполняется оператором при помощи устройства (машины или механизма), подающего электродную проволоку в зону сварки.
Автоматическая сварка осуществляется без участия человека. При этом механизируются операции по получению сварного шва по заданной программе.
По способу защиты металла различают: сварку в воздухе, в вакууме, в среде защитных газов, под слоем флюса, в пене и т. п.
Общая схема методов сварки плавления (рис. 1) может быть представлена рядом последовательных стадий состояния металла в зоне сварки:
1 – элементы собраны под сварку и закреплены в необходимом положении относительно друг друга. Между элементами остается зазор. В зоне стыка полностью отсутствуют химические связи;
2 – на поверхность металла в зоне стыка воздействуют мощным концентрированным потоком тепловой энергии Q. Подведенный тепловой поток нагревает кромки материала выше температуры плавления. Расплавленный металл обеих кромок сливается, образуется общая ванночка из жидкого металла (сварочная ванна). Ванночка удерживается на частично оплавленных кромках. Зазор между заготовками исчезает. Химические связи в жидком металле близки к химическим связям твердого тела, поэтому эту стадию принято называть образованием физического контакта;
3 – при прекращении теплового воздействия на кромки свариваемых элементов (выключение источника тепла или перемещение его вдоль кромок) зона сварки охлаждается за счет передачи теплоты вглубь свариваемых элементов и в окружающую среду. Происходит кристаллизация сварочной ванны с образованием литой структуры шва, т. е. создание химических связей по сечению свариваемого соединения. Частично оплавленные зерна основного металла на границе сварочной ванны являются основанием для «пристройки» атомов из жидкости для кристаллизации шва.
Рис. 1. Схема стадий образования соединения сваркой плавлением:
1 – сборка под сварку;
2 – образование сварочной ванны под воздействием теплоты;
3 – кристаллизация ванны с образованием сварного соединения;
4 – макроструктура зерен на границе шва.
Рассмотрим основные виды сварки плавлением.
Газовая сварка
Газовой сваркой называется сварка плавлением с использованием теплоты горючих газов.
Для плавления металлов используют тепло пламени смеси газов и кислорода, сжигаемых с помощью специальной горелки.
Газовая сварка классифицируется по виду применяемого горючего газа:
• ацетилено-кислородная сварка;
• керосино-кислородная сварка;
• бензино-кислородная сварка;
• пропанобутано-кислородная сварка.
Сущность процесса газовой сварки (см. схему газовой сварки, рис. 2) заключается в том, что свариваемый и присадочный металлы расплавляются за счет тепла пламени (4) горелки. При этом кромки свариваемых заготовок (1) расплавляются, а зазор между ними заполняется присадочным металлом (2), который вводят в пламя горелки (3) извне. В качестве горючих газов применяются природные газы, нефтяные газы, а также водород, ацетилен, пары керосина и бензина и др. Наибольшее распространение получили сварка с использованием ацетилена, паров бензина, паров керосина, пропанобутана.
Рис. 2.
Схема газовой сварки
В процессе сварки металл соприкасается с газами пламени, а вне пламени – с окружающей средой (воздухом) или специально созданной газовой средой. В результате металл подвергается значительным изменениям. Наибольшим изменениям подвергается металл, расположенный в зоне сварочной ванны. При этом изменяется содержание примесей и легирующих добавок в металле. Одновременно металл в зоне сварки обогащается кислородом, водородом, азотом, углеродом. Для предотвращения процессов окисления и извлечения из жидкого металла сварочной ванны окислов и неметаллических включений применяются флюсы.
Расплавленный металл сварочной ванны представляет сплав основного и присадочного металлов. По мере удаления пламени горелки металл кристаллизуется в остывающей части ванны. Закристаллизовавшийся металл сварочной ванны образует металл шва. Шов имеет структуру литого металла с вытянутыми укрупненными кристаллами, направленными к центру шва.
В настоящее время в промышленности из множества видов газопламенной обработки металлов наибольшее применение получили газовая сварка, газовая пайка, кислородная резка.
Газы, применяемые при газовой сварке, резке и пайке
Кислород (О2)
При нормальном атмосферном давлении и обычной температуре кислород представляет собой газ без запаха, цвета и вкуса. Он несколько тяжелее атмосферного воздуха. При нормальном атмосферном давлении и температуре 20 °C масса 1 м3 кислорода равна 1,33 кг. Горючие газы при сгорании с кислородом дают высокую температуру. Сам кислород не горюч, не токсичен, не взрывоопасен, но является сильнейшим окислителем, резко увеличивающим способность других веществ к горению, а при определенных условиях – к взрыву.
В земной атмосфере находится около 20 % кислорода. Поэтому кислород получают из атмосферного воздуха на специальных установках методом ректификации. Например, на кислородных станциях воздух очищают от пыли, влаги и углекислоты. Далее очищенный воздух сжимается компрессором до высокого давления и охлаждается в теплообменниках до сжиженного состояния. Жидкий воздух разделяют на кислород и азот. Процесс разделения происходит вследствие того, что температура кипения жидкого азота (–195,8 °C) ниже температуры кипения жидкого кислорода (–182,96 °C). Азот, являясь более легкокипящим, испаряется первым. С помощью кислородного компрессора чистый кислород подают под давлением 15 МПа (150 кгс/см2) в специальные кислородные баллоны. Полученный технический кислород должен соответствовать ГОСТу 5583–78. В зависимости от сорта содержание чистого кислорода колеблется от 99,5 до 99,7 %. Баллоны с кислородом окрашивают в синий цвет с черной надписью «кислород» и используют только для кислорода. Температурный диапазон использования сжатого кислорода от –50 до +30 °C. Запрещается хранение и транспортировка наполненных баллонов при температуре выше 60 °C.
Баллоны возвращают на заполнение с остаточным давлением не ниже 0,05 МПа (0,5 кгс/см2).
Водород (H2)
Газ без цвета и запаха. В смеси с кислородом водород образует взрывчатую смесь – гремучий газ. Водород требует строгого соблюдения правил техники безопасности, т. к. он способен проникать через мельчайшие поры, образовывая с воздухом взрывчатые смеси. Водород получают электролизом воды или в специальных водородных генераторах путем воздействия серной кислоты на железную стружку или цинк. Водород хранится и транспортируется в стальных баллонах при максимальном давлении 15 МПа (150 кгс/см2). Температура его сжижения –253 °C. При сгорании водорода пламя не светится, и его зоны не имеют четких границ.
Пиролизный газ
Пиролизный газ представляет собой смесь газообразных продуктов термического разложения нефти, нефтепродуктов или мазута. Содержит вредные сернистые соединения, которые вызывают коррозию мундштука горелки. Эта смесь пиролизного газа требует тщательной очистки от сернистых соединений.
Нефтяной газ
Нефтяной газ представляет собой смесь горючих газов, являющихся побочным продуктом нефтеперерабатывающих заводов. Его применяют для сварки, резки и пайки сталей толщиной до 3 мм, а также сварки цветных металлов.
Природный газ
Природный газ получают на газовых месторождениях. Природный газ состоит в основном из метана (до 82–93 %). Хранят и транспортируют в баллонах, в сжиженном виде. Для определения утечек в газ добавляют специальные ароматизаторы.
Пропанобутановая смесь
Пропанобутановую смесь получают при добыче и переработке естественных нефтяных газов и нефти. Хранят и транспортируют в сжиженном состоянии в баллонах емкостью 40 или 55 литров при давлении 1,6–1,7 МПа. Жидкой смесью наполняют только половину баллона, т. к. при нагреве смесь значительно расширяется, что может привести к взрыву.
Пропан и бутан тяжелее воздуха и имеют неприятный запах.
Керосин и бензин
При газопламенной обработке металлов керосин или бензин используют в виде паров.
Для этой цели в горелке или в резаке имеются специальные испарители, нагревающиеся от вспомогательного пламени или электрическим током.
Ацетилен
Ацетилен получил наибольшее распространение благодаря таким важным свойствам, как высокая теплотворная способность, высокая температура пламени. Ацетилен представляет собой химическое соединение углерода и водорода (С2Н2). Это бесцветный газ с характерным запахом из-за наличия примесей сероводорода, фтористого водорода и пр. Длительное вдыхание ацетилена вызывает тошноту, головокружение, иногда сильное общее отравление. Ацетилен легче воздуха. Ацетилен относят к взрывоопасным газам. Температура воспламенения лежит в пределах 240–630 °C и зависит от давления и присутствия различных примесей. Ацетилен взрывоопасен при давлении 0,145–0,16 МПа; при нагревании в диапазоне 240–630 °C и при наличии 2–80 % ацетилена в смеси с воздухом; при наличии 2–93 % ацетилена в смеси с кислородом.
Взрыв ацетиленокислородной или ацетиленовоздушной смеси может произойти от искры, пламени или при сильном местном нагреве. Потому ацетилен требует осторожности и строгого соблюдения правил безопасности.
При промышленном способе ацетилен получают воздействием электродугового разряда на жидкое горючее: нефть, керосин. Применяется также способ промышленного производства ацетилена из природного газа метана. Для этого смесь метана с кислородом сжигают в специальных реакторах при температуре 1300–1500 °C. Из полученной смеси газов с помощью растворителя извлекается концентрированный ацетилен. Получение ацетилена промышленным способом на 30–40 % дешевле, чем получение его из карбида кальция. Ацетилен, полученный промышленным способом, закачивают в баллоны, где он находится в порах специальной массы, растворенной в ацетоне.
Рабочее давление сжатого ацетилена не должно превышать 1,9 МПа (19 кгс/см2).
Остаточное давление в наполненном баллоне при температуре 20 °C должно быть в пределах 0,05–0,1 МПа (0,5–1,0 кгс/см2). Для сохранности наполнительной массы запрещается отбирать ацетилен из баллона со скоростью более 1700 дм3/час.
Ацетилен также получают из карбида кальция в специальных генераторах путем взаимодействия его с водой. Потребительские свойства ацетилена не зависят от способа получения. Карбид кальция получают путем сплавления кокса и обожженной извести в электродуговых печах при температуре 1900–2300 °C. Расплавленный карбид кальция сливают из печи в формы-изложницы, где происходит его остывание. После дробления карбид кальция сортируют на куски размером 2–80 мм. Карбид кальция очень активно впитывает влагу из воздуха, поэтому его хранят и транспортируют в герметически закрытой таре: барабанах или банках из кровельной жести по 40/100/130 кг.
Из 1 кг карбида кальция получают 235–280 литров ацетилена. Теоретически на 1 кг карбида кальция необходимо 0,56 литра воды. Практически берут 5–20 литров воды для охлаждения газогенератора и безопасной работы. Запрещается для исключения взрыва использовать мелкий и пылевидный карбид кальция.
В таблице 2 приведены характеристики газов, применяемых для газовой сварки.
Таблица 2
Характеристики газов, применяемых для газовой сварки
Материалы и оборудование для газопламенной обработки металлов:
• кислород и горючий газ в специальных баллонах или генератор для его получения;
• аппаратура управления (редукторы, манометры);
• сварочные горелки или резаки в комплектах со шлангами для подачи газов;
• присадочная проволока для сварки или наплавки;
• очки-светофильтры с затемненными стеклами;
• набор инструментов: молоток, набор ключей для баллонов и горелок, стальные щетки, костюм для сварщика и перчатки;
• сварочный стол или приспособления для сборки и фиксации деталей;
• инструменты для измерения и разметки;
• средства пожаротушения.
Достоинства газовой сварки:
• простота и дешевизна оборудования;
• дешевые расходные материалы;
• простой способ регулирования процесса горения;
• маневренность в применении (любое положение горелки в пространстве);
• высокая технологичность использования;
• энергонезависимость от источников питания.
Недостатки газовой сварки:
• низкая эффективность нагрева;
• широкие швы и широкая зона термического влияния;
• относительно низкая производительность труда;
• трудность автоматизации процесса.
Электрическая дуговая сварка
Источником теплоты при дуговой сварке служит электрическая дуга, которая горит между электродом и заготовкой. В зависимости от материала и числа электродов, а также способа включения электродов и заготовки в цепь электрического тока различают следующие способы дуговой сварки:
• по применяемым электродам – дуга с плавящимся и неплавящимся электродом;
• по степени сжатия дуги – свободная и сжатая дуга;
• по схеме подвода сварочного тока – дуга прямого и косвенного действия;
• по роду тока – дуга постоянного и переменного тока;
• по полярности тока – дуга на прямой полярности и дуга на обратной стороне полярности;
• по виду статистической вольт-амперной характеристики – дуга с падающей, возрастающей или жесткой характеристикой;
• по способу защиты сварного шва – в среде защитного газа или под слоем флюса.
Сварочной дугой называют устойчивый длительный разряд электрического тока в газовой среде между находящимися под напряжением твердыми или жидкими проводниками (электродами) либо между электродом и изделием.
Сварочная дуга существует при токах от десятых долей ампера до сотен ампер. Дуга характеризуется высокой плотностью тока в электропроводном газовом канале, выделением большого количества тепловой энергии и сильным световым эффектом.
Разряд является концентрированным источником теплоты и используется для расплавления металла при сварке. Дуговой разряд тока происходит в ионизированной атмосфере газов и паров металла. Ионизация дугового промежутка происходит во время зажигания дуги и непрерывно поддерживается в процессе ее горения.
Электрические заряды в сварочной дуге переносятся положительно и отрицательно заряженными частицами. Отрицательный заряд несут электроны, а положительный и отрицательный заряды – ионы. Процесс, при котором в газе образуются положительные и отрицательные ионы, называется ионизацией, а газ называется ионизированным.
Газы, в том числе и воздух, при нормальных условиях не проводят электрического тока. Это объясняется тем, что при нормальных условиях, т. е. при нормальном атмосферном давлении и температуре воздуха 20 °C, воздушная среда состоит из нейтральных молекул и атомов, которые не являются носителями зарядов. Эти молекулы и атомы станут электропроводными в том случае, если в своем составе будут иметь электроны, которые возникают при воздействии на них электрического тока.
Для возникновения электропроводности газов они должны быть ионизированы.
Ионизацией молекулы (атома) называется отщепление одного или нескольких электронов и превращение молекулы (атома) в положительный ион. Если молекулы (атомы) присоединяют к себе электроны, то возникают отрицательные ионы.
Ионизация газа вызывается внешними воздействиями:
• достаточным повышением температуры;
• воздействием различных излучений;
• действием космических лучей;
• бомбардировкой молекул (атомов) газа быстрыми электронами или ионами.
Обратный ионизации процесс, при котором электроны, присоединяясь к положительному иону, образуют нейтральную молекулу (атом), называется рекомбинацией.
При обычных температурах ионизацию можно вызвать, придав уже имеющимся в газе электронам и ионам при помощи электрического поля большие скорости. Обладая большой энергией, эти частицы могут разбивать нейтральные атомы и молекулы на ионы. Кроме того, ионизацию можно вызвать, воздействуя световыми, ультрафиолетовыми, рентгеновскими лучами, радиоактивным излучением.
Однако, исходя из практической точки зрения и в целях безопасности использования, применяют другие способы ионизации.
Так как в металлах имеется большая концентрация свободных электронов, то можно извлечь эти электроны из объема металла. Существует несколько способов извлечения электронов из металла.
Для сварки электрической дугой имеют значение два способа:
• термоэлектронная эмиссия, при которой происходит «испарение» свободных электронов с поверхности металла благодаря высокой температуре. Чем выше температура, тем большее число свободных электронов приобретает энергию, достаточную для преодоления потенциального барьера в поверхностном слое и выхода из металла.
• автоэлектронная эмиссия. При автоэлектронной эмиссии извлечение электронов из металла производится при помощи внешнего электрического поля. Приложенное извне электрическое поле изменяет потенциальный барьер у поверхности металла и облегчает выход электронов, имеющих большую энергию и могущих преодолеть этот барьер.
Ионизацию, вызванную в некотором объеме газовой среды, принято называть объемной ионизацией. Объемная ионизация, полученная благодаря нагреванию газа до очень высоких температур, называется термической ионизацией.
При высоких температурах газа значительная часть молекул обладает достаточной энергией для того, чтобы при столкновениях могло произойти разбиение нейтральных молекул на ионы. Кроме того, с повышением температуры общее число столкновений между молекулами увеличивается. При очень высоких температурах в процессе ионизации заметную роль играет излучение от электродов и излучение от газа.
Прохождение электрического тока через газы называется электрическим разрядом.
Дуговой разряд является одним из видов электрического разряда.
Существуют и другие виды электрического разряда в газах:
• искровой кратковременный разряд, который происходит при мощности источника питания, недостаточной для поддержания устойчивого дугового разряда;
• коронный разряд, возникающий в неоднородных электрических полях и проявляющийся в виде свечения ионизированного газа;
• тлеющий разряд, который возникает при низких давлениях газа (например, в газосветных трубках).
Для сварки металлов применяется, в основном, электрическая дуга прямого действия, т. е. используется дуговой разряд между изделием и электродом. В такой дуге одним электродом является металлический или угольный стержень, а вторым – свариваемое изделие.
К электродам подводится питание – электрический ток. Ток вырабатывается специальным устройством – источником питания. Источники питания вырабатывают переменный или постоянный ток. В дуге выделяют несколько областей (рис. 3):
1 – катод;
2 – катодная область;
3 – столб дуги;
4 – анодная область;
5 – анод.
Рис. 3. Основные области электрической дуги и распределение потенциала в дуге
Каждая из выделенных областей отличается своими физическими явлениями, протекающими в ней. Участки, непосредственно примыкающие к электродам, называют, соответственно, анодной и катодной областями. Положительный электрод – анод, а отрицательный электрод – катод. Длина анодной и катодной областей очень мала – от нескольких длин свободного пробега нейтральных атомов в катодной области – 110–5 см и до длины свободного пробега электрона в анодной области – 110–3 см. Между этими областями располагается наиболее протяженная высокотемпературная область (0,05–0,5 см) разряда – столб дуги.
Распределение электрического потенциала по длине дуги неравномерное. Возле электродов имеют место скачки падения потенциалов, вызванные условиями прохождения электрического тока на границе между ионизированным газом и металлическими электродами. Дуговой разряд обязан своим существованием процессам на катоде. Катод является «поставщиком» электронов. Причины выхода электронов – в существовании термоэлектронной и автоэлектронной эмиссии, упоминавшейся выше.
Электроны, эмитированные из катода, ускоряются под действием электрического поля. На внешней границе катода электроны сталкиваются с молекулами и атомами газа, находящегося в межэлектродном пространстве. При упругих столкновениях при попадании электронов в молекулы повышается температура газа. При неупругих столкновениях электроны, передавая частицам энергию, производят ионизацию газа.
В результате интенсивной термической ионизации столб дуги представляет собой ионизированный газ, состоящий из электронов и ионов – плазму. Под действием приложенного электрического поля электроны движутся к аноду, а положительно заряженные ионы – к катоду.
В результате интенсивной бомбардировки поверхностей электродов ионами и электронами происходит мгновенное разогревание металла. При этом 43–43 % общей подводимой мощности выделяется на аноде, 36–38 % выделяется на катоде, 20–21 % мощности уходит в окружающую среду через излучение и конвекцию паров и газов, а остальные потери мощности – на разбрызгивание и угар свариваемого металла. При сварке, как правило, анодом служит свариваемая деталь.
При сварке угольным электродом температура в катодной области достигает 3200 °C, в анодной области 3900 °C. При сварке металлическим электродом температура катодной области составляет 2400 °C, а анодной – 2600 °C. В столбе дуги температура достигает 6000–7000 °C.
Различная температура анодной и катодной областей используется для решения технологических задач. Например, при сварке тонколистовых металлов катодом является сама деталь, а анодом – электрод.
Зажигание (возбуждение) и горение электрической дуги
Процесс зажигания электрической дуги можно разделить на три этапа (рис. 4):
• короткое замыкание электрода на заготовку;
• отвод электрода на расстояние 3–6 мм;
• возникновение устойчивого дугового разряда.
Короткое замыкание (рис. 4а) выполняется для разогрева торца электрода 1 и заготовки 2 в зоне контакта с электродом. После отвода электрода (рис. 4б) с его разогретого торца (катода) под действием электрического поля начинается термоэлектрическая эмиссия электронов 3.