Большая энциклопедия техники Коллектив авторов
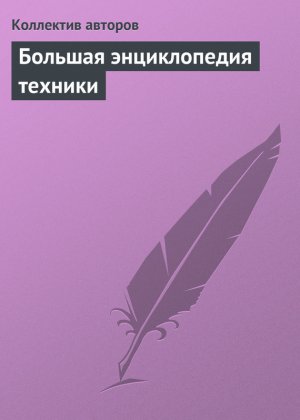
Опыливатель
Опыливатель – навесное орудие или аппарат для опыления сельскохозяйственных культур порошкообразными пестицидами.
Различают два типа опыливателей: с механической подачей порошка через дозатор и с пневматической подачей или просасыванием порошка через дозатор воздухом. По виду привода опыливатели бывают ранцевыми, ручными или тракторными навесными.
Опыливатели ОШУ-50, ОПС-30Б предназначены для обработки садов, лесополос, виноградников, а также зерновых, овощных и технических культур. Опыливатель состоит из рамы с кронштейнами для навески на трактор. Основным узлом является бункер, выполненный из листовой стали. Его стенки имеют наклон, чтобы не образовывалось зависаний порошка ядохимиката. Также для исключения зависания порошка в бункерах установлены лопастные мешалки (рыхлители). По своей конструкции они могут быть различными. Для подачи порошка к дозатору служат питающие устройства. Они могут быть механическими (шнеки, лопастные катушки у ОШУ-50) и пневматическими, когда порошок через дозатор засасывается воздушным потоком, создаваемым вентилятором (ОПС-30Б). Дозатор представляет собой заслонку, перекрывающую выходное отверстие, ее положением управляет тракторист из кабины, ее роль – установка опыливателя на заданную норму расхода пестицида. Распылители бывают прямого и бокового дутья. Распылители прямого дутья наносят ядохимикат на листья растений сверху или с боков под листья из нескольких трубопроводов с распыливающими наконечниками. Такие распыливатели применяют при обработке пропашных культур и виноградников. Распыливающие устройства бокового дутья наносят пестициды сбоку из одного трубопровода с распыливающим наконечником. Взвесь порошка распространяется перпендикулярно по отношению к движению опыливателя. Такое распыливающее устройство применяют при обработке садов, лесополос, полевых культур. Распыливающие наконечники могут быть щелевидными, цилиндрическими, секирообразными, ложечными. Наконечник может быть и комбинированным – при обработке смоченным жидкостью порошком. Воздушный поток создается вентиляторами, которые захватывают ядохимикат и с воздухом направляют его на растения. Вентиляторы могут быть центробежными и осевыми. Также они могут иметь вертикальную ось вращения крыльчатки (ОПС-30Б) и горизонтальную ось (ОШУ-50). При вертикальной оси вращения крыльчатка находится над всасывающим окном вентилятора, и питатель не требуется. При горизонтальной оси вращения для подачи порошка необходимо шнековое или иное питающее устройство. Ширина захвата при обработке садов 1—2 ряда, виноградников 3—4 ряда, полевых культур – 100 м.
Основные узлы ручного опыливателя, служащего для обработки растений на небольших или труднодоступных участках, – бункер с питателем, вентилятор с приводной рукояткой, труба с распыливающим наконечником. Ручной опыливатель снабжается заплечными ремнями. Производительность его достигает 30 деревьев за 1 ч, или 0,1 га/ч.
У всех опыливателей единый принцип действия: порошок ядохимиката питателем подается из бункера к дозатору, через который порошок засасывается в вентилятор разрежением и выбрасывается воздушным потоком через распыливающее устройство на листья обрабатываемых растений.
Паровой культиватор
Паровой культиватор – навесные и прицепные орудия для сплошной обработки почвы – предпосевного рыхления и очистки паров от сорняков.
Культиватор имеет сварную раму прямоугольной формы, состоящую из двух поперечных брусьев, которые соединены между собой пятью продольными связями. На передний брус приварены скобы для соединения поводков с рабочими органами, также приварены подвеска и кронштейны для присоединения опорных колес. Навесное устройство состоит из подвески с раскосами и двух кронштейнов с пальцами, на которые надевают шаровые шарниры нижних тяг навески трактора. Верхняя его тяга соединяется с верхним концом подвески. К поперечному брусу навешиваются на нажимных штангах поводковые секции. На каждой нажимной штанге надета пружина, которая опирается на фигурную шпильку. Переставляя шпильку по отверстиям штанги, можно регулировать силу натяжения пружины на поводки и, соответственно, глубину хода отдельных лап. Стрельчатые лапы устанавливают в два ряда, а рыхлительные – в три. Рабочие органы обоих рядов должны идти на одинаковой глубине. Этого добиваются изменением длины верхней тяги механизма навески трактора. Качество работы также изменяют регулировкой угла наклона лапы. На культиваторе установлены автоматические пружинные предохранители, которые защищают лапы при обработке тяжелых и каменистых почв. Предохранитель состоит из обоймы, прижимающейся под действием пружины к эксцентриковой призме. При встрече лапы с камнем увеличивающееся сопротивление заставляет ее отклониться назад. После преодоления препятствия пружина возвращает лапу в исходное положение. Опорные колеса относительно рамы устанавливают таким образом, чтобы глубина хода рабочих органов по всему захвату была одинаковой. Опорные колеса с помощью рукоятки можно перемещать относительно рамы, увеличивая или уменьшая глубину хода рабочих органов. Рабочая ширина захвата культиватора 4 м, можно переоборудовать на 3 м. Культиваторы снабжаются комплектами сменных рабочих органов, в них входят плоскорежущие, универсальные и рыхлительные лапы. Плоскорежущие лапы могут быть как односторонними, так и двухсторонними, используемыми для подрезания сорняков. Двухсторонние плоскорежущие стрельчатые лапы имеют ширину захвата от 145 до 330 мм, угол между режущими кромками лапы составляет 60—70°. Односторонние плоскорежущие лапы-бритвы монтируются только на пропашных культиваторах. Универсальные лапы используют и для подрезания сорняков, и для рыхления почв. Они имеют ширину захвата от 220 до 385 мм. Глубина обработки – до 12 см. Рыхлительные лапы могут быть долотообразными, копьевидными односторонними и зубовидными двухсторонними. Долотообразная лапа рыхлит полоску почвы до 20 или на глубину до 16 см. Копьевидная односторонняя рыхлительная лапа имеет ширину 50 мм.
Прицепной гидрофицированный культиватор КПГ-4 используется для предпосевной обработки почвы с одновременным боронованием. Культиватор имеет приспособление для навески зубовых борон. Ширина захвата 4 м, глубина обработки почвы от 5 до 12 см. Стрельчатые и рыхлительные лапы расположены в три ряда на грядилях, в рабочее положение из транспортного переводятся выносным гидроцилиндром, работающим от гидросистемы трактора. Грядили крепятся к переднему брусу сварной рамы, установленной на двух пневматических колесах. На заданную глубину рабочие органы культиватора устанавливают перестановкой колес винтовым механизмом.
Прицепной культиватор КП-4А представлен в двух модификациях: с выносным гидроцилиндром и с механическим подъемом рабочих органов в транспортное положение. На культиваторе устанавливаются стрельчатые полольные лапы на пружинных стойках и присоединяются с помощью крюкообразных тяг зубовые бороны. У культиватора с гидравлическим подъемом и заглублением рабочих органов один квадратный вал, в середине которого закрепляется рычаг. На спице монтируется уголок, на переднем брусе рамы – коромысло. С уголком соединяется гидроцилиндр, а его шток – с коромыслом. Коромысло и рычаг на валу связаны тягой. При втягивании штока в цилиндр лапы заглубляются. Глубина хода регистрируется перестановкой упорной шайбы, стоящей на штоке поршня гидроцилиндра. У культиватора с механическим подъемом лап на полуосях колес стоят два храповых автомата, каждый из которых поднимает половину рабочих органов. В систему подъемных механизмов включены компенсационные пружины, которые помогают автомату поднимать лапы и смягчать удары при их опускании. Ширина захвата культиватора 4 м.
Навесной культиватор ККН-2,25Б применяется для сложной обработки почв, засоренных камнями. Он комплектуется стрельчатыми универсальными лапами, смонтированными на жестких стойках с пружинными предохранителями. В комплект входят и рыхлительные лапы с окучниками. Глубина обработки почвы – 8—15 см. Ширина захвата культиватора 2,25 м. Качество работы культиваторов оценивают выдержанностью глубины рыхления, выровненностью обработки дна борозд, забиваемостью рабочих органов, чистотой подрезания сорняков.
Планировщик
Планировщик – прицепная машина для планировки (выравнивания поверхности).
Длинная рама планировщика впереди и сзади опирается на колеса. Продольная база составляет 12 м. Нагрузка от передней части рамы на передние колеса передается посредством тяговой рамы и гидроцилиндром подъема. Узел задних колес выполняется в виде каркаса, который шарнирно соединяется с основной рамой. Каркас связан со штоком гидроцилиндра, управляющим поворотом колес относительно рамы. При движении штока колеса откатываются или подкатываются под раму. При этом рабочие органы машины поднимаются в транспортное положение или опускаются в рабочее. Также управляет подъемом и опусканием планировщика и передний гидроцилиндр. На раме жестко закреплен основной орган планировщика – ковш, на задней стенке которого смонтирован сменный нож. Боковины ковша для устойчивости при движении по неровному участку опираются на лыжи. К поперечине основной рамы шарнирно присоединена рамка с вставными зубьями, она образует рыхлитель, для его управления служит гидроцилиндр.
При работе ковш режущей кромкой срезает грунт с повышенных мест, заполняется им и ссыпает его на пониженные участки, впадины поля и разравнивает его, устраняя таким способом неровности поверхности. Планировка осваиваемых и улучшаемых сенокосных угодий – обязательное мероприятие. Этими же машинами планируют трассы под оросительные каналы и дороги для движения дождевальных машин.
Пресс-подборщик
Пресс-подборщик – машина, используемая для сбора сена или соломы из валков и прессования их в тюки прямоугольной формы.
Пресс-подборщик состоит из прямоугольного устройства, прессующей части, вязального аппарата, механизмов передачи движения и регулировки, рамы и колес. Приемное устройство подбирает валки сена или соломы и подает их в прессовальную камеру. Одним из основных узлов приемного устройства является подборщик барабанного типа. На его валу закреплены диски, в которых посажены хвостовики державок с пружинными зубьями. Державки с зубьями вращаются с дисками вокруг вала и одновременно поворачиваются на некоторый угол вокруг своей оси, что достигается креплением на хвостовиках кривошипов с роликами. При вращении вала ролики катятся по фигурной дорожке другого диска и заставляют поворачиваться державки с зубьями на небольшой угол. Во время захвата сена или соломы зубья движутся по окружности, а в момент передачи в приемную камеру поворачиваются вокруг оси державок и опускаются. Это сложное движение позволяет зубьям плавно выходить из массы сена или соломы без затаскивания ее вниз. Вал и державка защищены кольцами-хомутами от наматывания на них сена или случайного повреждения. Вал подборщика получает вращение цепной передачей от вала контрпривода. К раме подборщик присоединен шарнирно и опирается на пневматические колеса. По высоте его положение можно регулировать рычажным механизмом, расположенным у колеса. В приемной камере смонтированы два упаковщика – передний и задний. Они направляют сено или солому порциями в прессовальную камеру. Передний упаковщик несет три рабочих зуба, а задний – два. Упаковщик выполнен в виде механизма с коромыслом с амортизационной пружиной, кривошипа и зубьев. Амортизационные пружины предотвращают поломки зубьев при возникновении на их пути препятствия. Если под упаковщики попадает большая порция сена или соломы, которую они не могут продвинуть в прессовальную камеру, пружины сжимаются, и зубья упаковщика отходят. Движение зубьев переднего упаковщика согласуется с движением поршня, оно регулируется соединением карданной передачи на кривошипный вал переднего упаковщика. От вала движение цепью передается на задний упаковщик. Движения зубьев обоих упаковщиков также должны быть согласованными. Это достигается определенным взаимным расположением кривошипов. Прессующая часть формирует и прессует тюки сена или соломы. Она состоит из прессовальной камеры с регулятором плотности, поршня и лотка. Прессовальная камера – это основание, на котором смонтированы все механизмы машины, передняя часть камеры опирается на спицу, а средняя – на ось ходовых колес. В конце камеры установлен регулятор плотности, которым можно изменить концевое сечение камеры и регулировать плотность спрессованных тюков. Расширению спрессованного сена препятствуют зубчатые задерживатели, расположенные в верхней части прямоугольной камеры с двух сторон. Они образуют в тюке пазы для укладывания обвязочной проволоки. Поршень при рабочем ходе, совершая в камере возвратно-поступательные движения, проталкивает сено вдоль камеры и прессует его. Сбоку к поршню прикреплен нож для обрезания охвостьев каждой порции сена или соломы. В его корпусе, выполненном из листовой стали, сделаны щели для прохода игл вязального аппарата. Перемещается поршень по направляющим салазкам прессовальной камеры, пальцем он соединен с головкой шатуна и приводится в движение от выходного вала редуктора главной передачи. Вязальный аппарат обвязывает сформированные тюки проволокой в два обхвата. Это самый ответственный узел машины. Тюки сена или соломы связываются стальной, термически обработанной проволокой диаметром 2 мм или специальным синтетическим шпагатом. Основными частями вязального аппарата являются две иглы, два игловязателя, механизмы включения и приводы. Цикл работы аппарата совершается за один ход поршня и состоит из четырех этапов: включение, подача проволоки или шпагата, образование узла и выключение.
1. Включается вязальный аппарат в тот момент, когда мерительное колесо совершает полный оборот. Прессуемое сено перемещается вдоль камеры и поворачивает мерительное колесо, у которого зубцы вдавлены в сено. Вращающийся вместе с мерительным колесом палец упирается в конец руки включения, ее другой конец освобождает собачку, под действием пружины она поворачивается и включает передачу на механизмы вязального аппарата. Ведущая часть привода находится в корпусе и получает движение цепью от звездочки общей передачи на звездочку привода аппарата. Муфта включения, имеющаяся на валу кривошипа, связывает в момент включения входной вал передачи и вал кривошипа. Выступ-упор, находящийся на внутренней поверхности ведущей части муфты, при повороте собачки связывает привод с валом кривошипа. При его вращении ролик, имеющийся на его конце, смещается по прорези кулисы и поворачивает рычаг, приводя тягой в движение иглы.
2. При движении иглы входят в пазы поршня, обтягивают тюк проволокой или шпагатом и ее концы помещают на крючки-узловязатели. Проволока огибает тюк со стороны поршня, ее конец иглой укладывается на пальцы-направляющие рядом с другим концом, уже зажатым в зажиме и обхватившим тюк. Поданный иглой конец проволоки перекусывается, зажимается, а другой – освобождается. На крючке-узловязателе остаются свободные концы. Иглы двигаются назад, а в зажиме остается конец проволоки для следующего тюка.
3. Крючки-узловязатели закручивают концы в узел. Одновременно в процесс включаются предохранительный крючок и прижим.
4. Предохранительный крючок оттягивает проволоку, чтобы ее не захватил крючок-узловязатель, а прижим натягивает ее для получения правильного узла.
В конце цикла работы собачка упирается в конец руки включения, поворачивается вокруг своей оси за счет инерции движущихся частей вязального аппарата и выключает передачу на вал кривошипа.
Связанный тюк соломы или сена проталкивается следом двигающимися тюками к выходу прессовальной камеры – на лоток, с которого сползает на землю. В аппарате имеется световая сигнализация для предупреждения тракториста об обрыве или полном использовании проволоки.
Рабочие органы пресс-подборщика приводятся в действие от вала отбора мощности трактора карданной передачей через маховик и редуктор главной передачи. В системе передач имеется ряд предохранительных устройств для предупреждения поломок во время перегрузок. Это предохранительные муфты храпового типа, срезные шпильки у маховика и у переднего упаковщика, предохранительный болт в приводе вязального аппарата, предохранительный упор поршня и нож кассет, амортизационный механизм упаковщика.
При движении трактора подборщик зубьями подбирает валок сена или соломы и подает его в приемную камеру. Упаковщики подхватывают порции сена или соломы и отправляют их в прессовальную камеру. Поршень, совершая движение назад, к маховику, освобождает окно в прессовальную камеру, и происходит передача порции сена в нее. При движении в обратном направлении поршень обрезает ножом охвостья, отделяет одну порцию сена от другой, перемещая их вдоль прессовальной камеры, формуя тюк сена или соломы прямоугольного сечения. Камера снабжена специальными зубьями для того, чтобы во время холостых ходов поршня (к маховику) удерживать очередные порции сена в спрессованном виде.
При движении сена в прессовальной камере последующие порции поворачивают мерительное зубчатое колесо. За один его оборот сформованный тюк сена доводится до необходимой плотности, при этом происходит включение вязального аппарата, который подает проволоку или шпагат и образует по два узла на каждом тюке, после чего выключается до следующего цикла. Тюки, связанные в два обхвата, продвигаются к выходу, поступают на лоток, по которому и опускаются на поверхность поля.
Пропашной культиватор
Пропашной культиватор – навесное орудие, используемое для междурядной обработки посадок картофеля и других пропашных культур (кукурузы, подсолнечника).
Культиватор КОН-2,8ПМ рассчитан на обработку четырех рядов картофеля с междурядьями 60 и 70 см, КРН-3,6-4,2 также на обработку четырех рядов картофеля, но с междурядьями 90 см или шести рядов с междурядьями 60 и 70 см. Культиватор ОКП-3А применяют для обработки трех рядов картофеля с междурядьями 60 и 70 см. Наиболее распространены первые два культиватора.
Культиватор КОН-2,8ПМ состоит из рамы с подвеской и опорными колесами, пяти секций с рабочими органами и копирующими колесами. Рама представляет собой брус квадратного сечения, к которому приварены две стойки с отверстиями для соединения с верхней тягой навески трактора и два кронштейна с пальцами для присоединения нижней тяги навески. К кронштейнам крайних секций присоединяются опорные колеса, обеспечивающие при работе горизонтальное расположение рамы над поверхностью поля. Культиватор снабжается сетчатой бороной, кронштейны которой тоже укрепляются на брусе, набором других рабочих органов для подрезания сорняков, рыхления почвы в междурядьях, окучивания и подкормки растений минеральными удобрениями. Каждая секция культиватора состоит из шарнирно связанных верхней тягой переднего и заднего кронштейнов, смонтированных на нижней рамке. Стойки рабочих органов закрепляются в держателях стопорными болтами. Основными рабочими органами являются окучники и ротационные боронки. Окучники используют для уничтожения сорняков на дне борозды, присыпания обрабатываемых растений рыхлой почвой и ее распределения по поверхности гребня. Более распространены окучники, состоящие из корпуса с носком и раздвижных крыльев. Крылья устанавливаются на различной высоте, изменяя положение распорки. Во время движения в междурядье окучник поднимает и раздвигает корпусом почву в обе стороны, в середине образуется борозда, а крыльями почва присыпается к рядам растений. Для лучшего подрезания сорняков и увеличения толщины разрыхленной почвы на корпус окучника вместо носка можно укрепить универсальную стрельчатую лапу, а к укороченным крыльям приварить прутки, которые образуют своеобразную решетку.
Укороченные крылья будут предотвращать сильное разбрасывание почвы в стороны во время работы на больших скоростях, и часть земли будет просыпаться сквозь прутковую решетку. Для боронования посадок картофеля до и после всходов на гребнях различной высоты используется ротационная универсальная боронка БРУ-0,7. Ее секция состоит из двух зубовых полусекций, связанных кронштейном, шарнирно соединенным с поводком. Секция бороны навешивается на основные секции культиватора. Заглубление секции осуществляется нажимной штангой. Полусекция состоит из конической и цилиндрической частей с зубьями. Во время боронования зубья сцепляются с почвой, и за счет этого полусекции вращаются, рыхлят почву и вычесывают сорняки на вершине и склонах гребней. Во время боронования по всходам цилиндрические части с полусекций снимают. Конструкция культиватора позволяет перемещать секции с рабочими органами по брусу и устанавливать их на обработку междурядий определенной ширины. Для осуществления подкормки минеральными удобрениями на культиватор устанавливаются туковысевающие аппараты с тукопроводами и подкормочными ножами. Привод осуществляется цепной передачей от опорных колес. При подъеме культиватора в транспортное положение вращение колес прекращается и высев удобрений приостанавливается.
КРН-4,2 устроен примерно по такой же схеме, он рассчитан на обработку картофеля, высаженного сажалками, имеющими рабочий захват 3,6 и 4,2 м. Этот культиватор используется и для обработки кукурузы, подсолнечника и других пропашных культур. При подготовке культиваторов к работе обращают особое внимание на формирование стыковых междурядий, образующихся на стыке двух соседних проходов сажалки по полю. Их обрабатывают обычно за два прохода культиватора крайними рабочими секциями. Если стыковые междурядья попадут внутрь захвата культиватора, то растения будут повреждены.
Разбрасыватель органических удобрений
Разбрасыватель органических удобрений – машина, предназначенная для разбрасывания компостов, торфокрошки и других органических удобрений.
Различают прицепы-разбрасыватели, разбрасыватели удобрений из куч, разбрасыватели жидких удобрений.
Прицеп-разбрасывателеь 1-ПТУ-3,5 состоит из рамы с ходовыми колесами, кузова с питающим транспортером, разбрасывающего устройства и механизма привода. Сварная рама имеет прицепное устройство, к нему шарнирно крепится опорная стойка, которая на стоянках используется как третья точка опоры, так как прицепы одноосные. После соединения прицепа с трактором стойка поднимается и фиксируется. Кузов разбрасывателя цельнометаллический. Боковые борта на петлях, могут открываться и в наклонном положении закрепляться. Для того чтобы удобрения не выбрасывались в сторону трактора, передний борт наращивается съемным задним бортом. Транспортер состоит из четырех сварных калиброванных цепей с металлическими планками, он монтируется на дне бункера. Цепи транспортера объединяются попарно. Каждая из двух ветвей имеет свое натяжное устройство, состоящее из вала, перемещающегося натяжными болтами, на котором свободно вращаются ведомые ролики цепей. Цепи разборные, они состоят из отдельных участков по девять звеньев, которые соединяются специальными звеньями, к ним пайками крепятся штампованные металлические планки. Каждая ветвь имеет по двадцать три планки. Ведущий вал со звездочками для всех цепей общий. Разбрасывающее устройство состоит из двух барабанов. Нижний барабан со шпорообразной поверхностью – измельчающий, он установлен в кузове; верхний шнекообразный барабан – разбрасывающий, он вынесен за пределы кузова прицепа. Такая конструкция барабанов полностью исключает заклинивание между ними твердых предметов, хорошо измельчает длинносоломистые включения навоза и обеспечивает их разбрасывание на ширину до 5 м. Рабочие органы прицепа-разбрасывателя приводятся в действие от вала отбора мощности трактора. Движение передается карданным валом через продольный вал с предохранительной муфтой на конический двухступенчатый редуктор, установленный на балках рамы. От него один вал цепной передачей вращает нижний барабан, а от него цепью в действие приводится верхний барабан. Другой вал редуктора сообщает движение храповому механизму привода питающего транспортера, он дает возможность регулирования скорости движения транспортера, изменения нормы внесения удобрений. На валу редуктора жестко посажен кривошип, в его пазу установлен палец шатуна. Устанавливая его на разном расстоянии от вала, можно менять радиус кривошипа. На ведущем валу транспортера на шпонке посажено храповое колесо. С двух его сторон на вал надеты две щеки, они связаны осью, на которой посажены ведущая собачка и шатун. Зуб собачки под действием пружины прижат к зубчатой поверхности храпового колеса. При смещении шатуна щеки совершают колебание, поворачиваются на определенный угол. Собачка, зацепленная с храповым колесом, поворачивает его и заодно вал транспортера на точно такой же угол. При обратном движении щек собачка проскакивает по храповому колесу, удерживаемому от перемещения второй собачкой. Чем больше радиус кривошипа, тем больше ход у питающего транспортера и тем больше удобрений сможет разбросать машина. Ее можно переоборудовать для внесения минеральных удобрений и извести с помощью съемного приспособления с резиновым кольцевым метателем. Промышленностью выпускаются большегрузные прицепы-разбрасыватели с грузоподъемностью 10-16Т: ПРТ-10 и РПБ-16.
Разбрасыватель РУН-15А состоит из валкообразователя, активного рабочего органа, роторного разбрасывателя, механизма подъема валкообразователя и системы передач. Валкообразователь состоит из двух боковых и задней стенок (подобно бульдозерной навеске) и навешивается спереди трактора. При работе боковые стенки опираются на катки. В задней стенке есть дозирующее окно, его размер и, соответственно, форму валка можно изменять специальными заслонками. В дозирующее окно удобрение направляет активный рабочий орган, состоящий из двуплечего рычага, на одном конце которого находится толкатель, а на другой действует гидроцилиндр с золотниковым приводом. Толкатель разбивает крупные комья удобрений, способствуя формированию непрерывного валка. Сзади трактора навешивается роторный разбрасыватель, который состоит из двух роторов и двух опорных катков. Роторы приводятся во вращение от вала отбора мощности трактора через карданный вал, одноступенчатый редуктор и две цепные передачи, они разбрасывают валок удобрений по обеим сторонам трактора. Разбрасыватель имеет рабочую ширину до 20 м. Его можно применять и для растаскивания удобрений из буртов в кучи. Дозирующее окно закрывают заслонками, а разбрасывающее устройство поднимают – таким способом машина переоборудуется в бульдозер.
Заправщик-жижеразбрасыватель вакуумный 3ЖВ-1,8 предназначается для откачки из жижесборников навозной жижи и ее транспортировки в поле с последующим разбрасыванием по поверхности почвы. Жижеразбрасыватель состоит из одноосного шасси на пневматических колесах, цистерны, заборного шланга, напорно-вакуумной системы, эжектора, затвора, разливочного лотка, воздушной мешалки и уровнемера.
Цистерна емкостью 1,8 м3 выполнена из стали. Внутренняя ее поверхность покрыта антикоррозийной эмалью, спереди есть смотровое окно, сверху располагается горловина, сзади установлен двухсекционный затвор с двумя рычагами для заборного шланга и разливочного лотка. Заборный шланг армированный, гофрированный из прорезиненной ткани длиной 4 м, его диаметр 7,5 см. Разливочное устройство снабжено патрубком со сменными жиклерами, что позволяет регулировать норму внесения жидкости. Разлив можно прекратить из кабины трактора с помощью троса. К горловине цистерны приварен патрубок напорно-воздушной системы, он соединяется трубопроводом с эжектором, установленным на выпускной трубе трактора. Цистерна заполняется 7—10 мин, для этого необходимо закрыть кран разливочного устройства, открыть кран заборного шланга, опустить шланг в жижесборник, на эжекторе закрыть заслонку и увеличить частоту вращения вала двигателя трактора. Выпускные газы по патрубку попадут в сужающийся канал (диффузор), где их скорость станет еще больше. В колене создается вакуум, он по нагнетательно-вакуумной магистрали будет передаваться в цистерну, которая начнет заполняться жижей. Контролировать уровень заполнения можно через смотровое окно и по уровнемеру поплавкового типа. После заполнения цистерны затвор шланга закрывают и открывают заслонку эжектора. Во время разлива жидкости затвор разливочного устройства открывают, заслонки на эжекторе закрывают. Газы пойдут в колено и по напорно-вакуумной магистрали в цистерну, в которой в результате возникнет избыточное давление. Для перемешивания жидкости в цистерне имеется воздушная мешалка, выполненная в виде согнутой под углом 90° трубы с двенадцатью отверстиями, расположенными в два ряда. Нижний конец трубы заглушен, верхний выходит из цистерны, в нерабочем состоянии он закрыт пробкой. Во время перевозки жижи пробку открывают, эжектором создают в цистерне вакуум, воздух входит в отверстия мешалки, попадает в цистерну и перемешивает жидкость. Данная машина также может быть использована для приготовления компостов с навозной жижей и транспортирования различных химикатов, заправки ими машин.
Заправшик-жижеразбрасыватель ЗУ-3,6 по устройству, принципу работы и назначению аналогичен предыдущим. Отличие заключается в том, что заправочной штангой, состоящей из стояка, трубы, рукавов, механизма поворота и двух гидроцилиндров, управляет тракторист из кабины. Он опускает ее в жижесборник, оперируя рычагами, после заправки устанавливает ее на машину. В горловине цистерны имеется предохранительный клапан. Колеса снабжены колодочными тормозами.
Разбрасыватель жидких удобрений РЖУ-3,6 устанавливается на шасси машины ГАЗ-53А. Кроме предохранительного клапана, на крышке горловины цистерны имеется предохранительное устройство для автоматической остановки двигателя автомашины, если цистерна уже заполнена. Насос приводит в действие гидродвигатель. Напорно-вакуумная магистраль состоит из ротационно-вакуумного насоса и системы воздухопроводов с кранами, благодаря которым можно создавать вакуум для заправки или избыточное давление для разлива жижи. В цистерне – лопастная мешалка.
Разбрасыватели жидкого навоза РЖТ-4 и РЖТ-8 используются для транспортировки, перемешивания и сплошного поверхностного распределения жижи, для заправки машин различными рабочими жидкостями, для приготовления компостов, мойки машин и тушения пожаров. Это цистерны-полуприцепы, передней частью опирающиеся на гидрокрюк трактора, а задней – на пневматические колеса. Отличие от ранее рассмотренных агрегатов в том, что на них установлены два насоса: вакуумнасос для заправки и подающий центробежный насос для разлива удобрений. Оба насоса приводятся в действие от вала отбора мощности трактора через переключающую муфту. В цистернах устанавливается струйная гидромешалка, которая работает от центробежного насоса.
Садовый плуг
Садовый плуг – прицепное орудие, предназначенное для вспашки почвы между рядами деревьев в садах на глубину до 25 см.
Плуг трехкорпусный, каждый корпус состоит из лемеха, отвала и полевой доски, прикрепленных к стойке. Имеются предплужники, которые, как и корпус, состоят из лемеха и отвала, укрепленных на стойке. Перед последним корпусом установлен дисковый нож. Рама плуга грядильная, собрана на болтах. На раме смонтирован брус жесткости. Для перевода плуга из рабочего состояния в транспортное применяется гидроцилиндр. Садовый плуг должен близко подходить к стволам деревьев, трактор двигается посередине ряда, чтобы не повредить кроны деревьев. С этой целью в садовых плугах делают прицепы специальной конструкции, позволяющие смещать плуг относительно трактора.
При движении плуга дисковый нож отрезает пласт почвы в направлении движения плуга, предплужник снимает верхний засоренный слой пласта и сбрасывает его в открытую предыдущим корпусом борозду. Лемех подрезает пласт снизу, слегка его поднимает, передает на отвал, который пласт оборачивает и крошит.
Свеклоуборочный комбайн
Свеклоуборочный комбайн – прицепное орудие, применяемое для уборки корнеплодов свеклы.
Применяют комбайны теребильного типа и комбайны с обрезкой ботвы на корню.
Трехрядный комбайн КСТ-3А предназначается для уборки свеклы, высаженной с междурядьями 45 см. Комбайн состоит из ботвоподъемников – по два на каждой секции теребильного аппарата; подкапывающих лап одностороннего действия, расположенных под секциями теребильного аппарата. В рабочей части лапы приварено перо-рыхлитель. Три секции теребильных аппаратов монтируются на подвижной раме. Аппарат выполнен в виде замкнутой цепи, к звеньям которой крепятся теребильные лапы. На концах лап для более надежного удержания свекольной ботвы имеются накладки. Раскрытие теребильных лап для захвата ботвы регулируется при помощи специальных устройств. На каждой секции установлено по одному выравнивателю. Каждый состоит из диска с конусными пальцами, опорного конуса, направляющей вилки, чистика и редуктора. Редуктор приводится в действие цепной передачей от вала теребильного аппарата. Режущий аппарат состоит из дискового ножа, закрепленного на валу, пружины, битера и редуктора. На комбайне поставлены элеватор ботвы, элеватор корней, шнековый транспортер-очиститель, погрузочный элеватор корней. Основная рама опирается на два пневматических ходовых колеса. Подвижная рама, на которой смонтированы основные рабочие органы, шарнирно связана с осями ходовых колес, а впереди опирается на два копирующих колеса. Из транспортного положения в рабочее и обратно подвижная рама переводится посредством гидроцилиндра, подключенного к гидросистеме трактора. Комбайн оборудован автоматическим устройством.
Двухрядный комбайн КСТ-2 используется для уборки сахарной свеклы с междурядьями 60 см. Комбайн имеет две секции рабочих органов. Основные рабочие органы по конструкции незначительно отличаются от комбайна КСТ-3. Вместо элеватора корней поперек машины устанавливается шнековый очиститель.
При движении комбайн направляется по рядкам автоматическим гидравлическим устройством. Отклонение рядков в поперечном направлении копирует копир-водитель. Ботвоподъемники поднимают полеглые листья и сжимают их в вертикальный пучок. В это время лапы подкапывают корни. Теребильные лапы аппарата теребят подкопанные корни свеклы из почвы за ботву, извлекают из почвы и направляют к выравнивателям, которые выравнивают головки свеклы и перемещают их с ботвой к режущему аппарату. Хвостовая часть корня поддерживается конусом, дисковый нож срезает ботву, она сбрасывается битером на элеватор ботвы, а корни падают на транспортер корней. Во время перемещения ботвы по элеватору почва с нее сквозь просветы просыпается, а ботва с помощью битера сбрасывается в прицепную тележку. Корнеплоды по элеватору перемещаются на шнековый очиститель. Сквозь просветы элеватора остатки ботвы и почвы просыпаются. На транспортере-очистителе происходит доочистка корнеплодов. Благодаря навивке спиралей шнека и частоте вращения корнеплоды получают вращательное движение, во время которого растительные остатки, мелкие корешки и почва затаскиваются в зазоры между шнеками. Корнеплоды перемещаются на погрузочный элеватор корней, а оттуда – в движущийся рядом транспортер.
Комбайн СКД-2 убирает свеклу, посеянную с междурядьями 45 и 60 см. Для направления комбайна по рядкам служит автоматическая система управления. На трубчатой раме, опирающейся на пневматическое колесо, установлен ботвосрезающий аппарат. Он состоит из двух копирующих механизмов и двух вращающихся дисковых ножей. Трубчатая рама шарнирно присоединена к основной раме. На трубчатой раме смонтировано выкапывающее и очистительное устройство, состоящее из двух дисковых копачей, вращающихся между ними резиновых бичей, шарнирно закрепленных на ступицах, и кулачкового очистителя корней. Также имеются шнековый очиститель, элеватор ботвы, элеватор корней, прицепное устройство, механизм передачи движения.
Комбайн СКД-2 можно использовать при уборке по двум схемам: направлять ботву в прицепную тележку, а корнеплоды – в кузов рядом движущегося транспорта; подавать ботву в бункер, периодически его разгружая, а корнеплоды – также в кузов транспорта, едущего рядом. При движении по полю опорное колесо ботвосрезающего аппарата копирует рельеф почвы, автоматически устанавливаются ножи ботвосрезающего аппарата на необходимую для среза высоту. Вращающиеся навстречу один другому дисковые ножи срезают головки с ботвой и бросают их на приемный транспортер, который перемещает их к битеру. Битер перетряхивает ботву и сбрасывает ее или в бункер, или на элеватор ботвы, откуда ботва сбрасывается в кузов идущего рядом транспорта. Дисковые копачи заглубляются в почву на глубину 8—12 см, поднимают пласт земли с корнеплодами. Пласт подвергается интенсивному крошению, почва просыпается, а корни с остатками почвы подвергаются воздействию резиновых бичей, которые очищают их от необрезанной ботвы, почвы, а затем выталкивают на кулачковый очиститель. Он выделяет остатки почвы, а корнеплоды транспортирует на шнековый очиститель, при перемещении по которому продолжается очистка. Затем переходный кулачковый вал подает корни на элеватор корней, выгружающий их в идущий рядом транспорт.
Сошник
Сошник – одна из основных сборочных единиц любой рядовой сеялки, служит для образования бороздки, в которую укладывает семена и заделывает их почвой.
Различают сошники дисковые и наральниковые.
Основа дискового сошника – литой корпус. В корпусе на осях, которые вращаются в подшипниках, установлены диски. Между корпусом и дисками стоят резиновые уплотнители. Между дисками и крышками дисков, в которых смонтированы подшипники, установлены картонные прокладки. Также в отверстия крышек ввинчены пробки, предохраняющие подшипники от загрязнения. В нижней части воронки корпуса переднего сошника укреплен направитель, на корпусе заднего сошника установлен изогнутый направитель. К корпусу сошника с помощью двух болтов и прижима прикреплены чистики для очистки налипшей с внутренней стороны дисков почвы. Диски устанавливают под углом 10° друг к другу, они образуют клин, который и формирует в почве борозду.
Дисковые сошники могут иметь иную конструкцию. Диски могут устанавливаться по отношению друг к другу под углом 18°. Корпус выполняется таким образом, что точка соприкосновения дисков будет находиться на уровне их горизонтальных диаметров впереди сошника. В итоге сошник будет при движении образовывать двойную бороздку с гребешком посередине. К корпусу с помощью болта крепится делитель с двумя рукавами. Идущий из семяпровода поток семян делится на две порции, которые и подаются на дно образуемых дисками двух бороздок. В передней части корпусов есть отверстие для закрепления поводков, присоединяющих сошники к сошниковому брусу.
Наральниковые сошники используют при работе на выровненных и хорошо разрыхленных почвах. Они бывают с острым и тупым углом вхождения в почву. Сошник с острым углом вхождения в почву имеет литой или изготовленный из листовой стали наральник, прикрепленный к передней части воронки. Наральник проводит в почве борозду. Его щеки поддерживают открытые стенки бороздки в верхней ее части. Сошник может быть с двумя воронками – одна для зерна, другая для удобрений. К воронкам присоединяется поводок, на его конец надевается грузик, который обеспечивает глубину хода сошника от 4 до 7 см. Поводками сошник шарнирно крепится на брусе рамы сеялки. Сошник с тупым углом вхождения в почву имеет узкий литой наральник. Он располагается под тупым углом к линии горизонта. Подобные сошники применяют для мелкой заделки семян. Воронка также заканчивается щеками. Внутри воронки имеется отражательная пластина, которая направляет на дно бороздки семена. Такие сошники устанавливают на зернотравяные сеялки СЗТ-3,6 и СУТ-47, а также льняные сеялки СУЛ-48 и СЛН-48А.
К брусу поводки сошников с валиками крепятся вкладышами. В брусе имеются дополнительные отверстия, которые используются при расстановке сошников на различную ширину междурядий. Для того чтобы сошники не забивались почвой, их устанавливают в два или три ряда, поэтому поводки сошников переднего ряда короче поводков сошников заднего ряда. Также поводки присоединены к механизму подъема и регулировки глубины их хода. Он устроен так: на раме сеялки укреплен квадратный вал подъема, с которым соединены штанги с пружинами при помощи вилок и скоб. Нижние концы штанг шплинтами связаны с поводками сошников, штанга относительно вилки перемещается, преодолевая сопротивление пружины. Изменяя сжатие пружины перестановкой шплинта в отверстия штанги, выравнивают ход сошника.
Наральниковые сошники с тупым углом вхождения в почву поводками крепятся к корпусам дисковых сошников. Передние концы поводков кронштейном закрепляются на тех же болтах, что и поводки дисковых сошников. Другими кронштейнами поводки крепятся к задним проушинам корпусов дисковых сошников. Глубина хода сошников, кроме грузиков, устанавливается винтом регулятора глубины, который монтируется на спице рамы сеялки. При вывертывании винта глубина хода уменьшается, при ввертывании – увеличивается. В гидрофицированных сеялках сошники поднимаются в транспортное положение и опускаются в рабочее с помощью выносного гидроцилиндра, который устанавливается на раме сеялки и включен в гидросистему трактора. Одновременно с подъемом сошников отключается передача на высевающие аппараты. При их опускании передача включается автоматически.
Трактор
Трактор – машина, которая может работать с прицепными, навесными и полунавесными орудиями, предназначается для широкого круга работ.
Тракторы подразделяются на сельскохозяйственные, лесохозяйственные, транспортные и промышленные. По типу ходовой части различают колесные, гусеничные и колесно-гусеничные тракторы. По типу двигателя они бывают дизельными, карбюраторными и газовыми. Также по величине номинальной силы тяги их делят на тяговые классы. Сельскохозяйственные тракторы, в свою очередь, подразделяются на тракторы общего назначения, пропашные, садовые, виноградоводческие, крутосклонные, горные и др. Тракторы общего назначения используются для вспашки, культивации, посева, уборки урожая, транспортных перевозок при отсутствии требований к величине дорожного просвета и колеи. У пропашных тракторов дорожный просвет (клиренс) увеличен, и их используют для обработки междурядий. Кроме этого, у них можно отрегулировать расстояние между серединами левого и правого колеса (колею). В садах, ягодниках, огородах применяют для выполнения различных работ универсальные пропашные тракторы. Они небольшие, у них регулируются дорожный просвет, колея и продольная база – расстояние между осями передних и задних колес. Виноградоводческие тракторы имеют небольшую ширину и высоту. На влажных, рыхлых и песчаных почвах используются колесные и гусеничные тракторы с повышенной проходимостью, у них все четыре колеса ведущие, а гусеницы имеют увеличенную опорную поверхность. Самоходное шасси характеризуется тем, что рабочее место водителя, двигатель и трансмиссия расположены у него в задней части, орудия прицепляются и навешиваются на часть рамы, расположенную между задним и передним мостом. Трактористу легче следить за ходом выполняемой работы, за действием рабочих органов навесных орудий, ему хорошо видны междурядья. На самоходные шасси можно устанавливать самосвальный кузов. Колея у них регулируемая.
Основными узлами трактора являются двигатель с пусковым устройством, трансмиссия, ходовой аппарат, рабочее оборудование и органы управления.
В двигателе сгорает топливо, и его химическая энергия переходит в механическую, возвратно-поступательное движение поршня заставляет вращаться коленчатый вал. От него крутящий момент передается трансмиссией к движителям ходового аппарата. Управляемая муфта сцепления позволяет временно разъединять коробку передач и двигатель перед выключением одной и включением другой передачи, а также плавно соединять двигатель и коробку передач. Неуправляемая соединительная муфта «гибкого» типа передает вращательное движение под некоторым углом, величину которого можно изменять. Временно увеличивать силу тяги трактора за счет снижения его скорости движения позволяет увеличитель крутящего момента. Это необходимо на труднопроходимых участках или во время начала движения трактора с тяжелым грузом. Коробка перемены передач необходима для изменения скорости движения трактора, его силы тяги, направления движения, отключения ходового аппарата от двигателя в момент его запуска или при работе двигателя во время остановки трактора. Конечная и промежуточная передачи позволяют передавать и увеличивать крутящий момент. Дифференциал дает возможность ведущим колесам трактора вращаться с разными скоростями. Трансмиссия гусеничных тракторов дифференциала не имеет, но вместо него есть механизм поворота. Остов трактора, образуемый корпусами двигателя и трансмиссии, опирается на ходовой аппарат непосредственно или через подвеску. У некоторых тракторов остов имеет вид рамы. Ходовой аппарат – это опора трактора, он преобразовывает вращательное движение ведущих колес в поступательное движение. Ходовой аппарат гусеничного трактора – бесконечная шарнирная лента, гусеница, по которой движется трактор. Гусеница имеет большую опорную поверхность, поэтому буксование у гусеничных тракторов меньше, чем у колесных. У колесных тракторов обычно задние колеса являются ведущими, а передние – направляющими. У тракторов повышенной проходимости передние колеса также являются ведущими. На задний мост колесных тракторов давит около 70—75% их веса, пневматические шины задних колес имеют больший диаметр, чем шины передних колес. Возможно распределение веса машины равномерно на оба моста (К-700, Т-150К), тогда все колеса делаются ведущими и имеют шины одинакового размера. Шины ведущих колес для лучшего сцепления с почвой имеют высокие почвозацепы и накачиваются несильно, а шины направляющих колес имеют большее внутреннее давление, что облегчает трактористу управление трактором, а также уменьшает износ шин. Для управления навесными, прицепными и полунавесными орудиями и машинами тракторы оборудуются гидравлической системой. Рабочие органы машин, агрегатируемых с трактором, приводятся в движение его валом отбора мощности. С помощью рулевого управления меняют положение передних колес и таким способом направляют движение колесных машин, у гусеничных – за счет уменьшения скорости вращения одной гусеницы относительно другой при помощи управляемой фрикционной муфты сцепления или планетарного механизма, включенных в трансмиссию трактора. Тракторы Т-700, Т-150К имеют раму, состоящую из двух частей, шарнирно соединенных так, что части рамы поворачиваются друг относительно друга в вертикальной и горизонтальной плоскостях. Передняя часть рамы, несущая двигатель, коробку передач и другие агрегаты, опирается на передний мост. На задний мост опирается, соответственно, задняя часть рамы, несущая на себе рабочее оборудование. Направление движения у таких тракторов изменяется при помощи гидросистемы путем поворота одной части рамы трактора относительно другой. Для остановки трактора или замедления скорости движения включают тормозную систему.
Триер
Триер (от фр. trier – «отбирать», «сортировать») – сельскохозяйственная машина для очистки от примесей семян зерновых культур и трав по длине частиц. Триер выделяет из семян очищаемой культуры длинные и короткие примеси. Триеры бывают цилиндрические и дисковые. В советских сельскохозяйственных предприятиях применялись в основном цилиндрические, в которых рабочим органом являлись ячеистые цилиндры. В цилиндрах, имеющих мелкие ячейки (так называемые кукольные), выделялись короткие зерна и примеси, а в цилиндрах с ячейками большего диаметра (овсюжных) – длинные зерна и примеси. При вращении цилиндра триера короткие зерна и примеси попадают в ячейки, поднимаются вверх и попадают в ячейки, поднимаются вверх и выпадают из ячеек в лоток. Длинные зерна и примеси идут с ходом по ячеистой поверхности. В Советском Союзе применялись такие машины (т. е. триеры), как БТ-5, имевшие производительность примерно 5 т/ч; БТ-20 – с производительностью около 20 т/ч.
Туковая сеялка
Туковая сеялка – машина, применяемая для сплошного внесения удобрений путем их разбрасывания по поверхности поля.
На сварной раме, основой которой является брус квадратного сечения, установлен металлический туковый ящик, закрытый сверху тремя полукрышками. Рама опирается на четыре пневматических колеса. Передние опорные колеса самоустанавливающиеся, задние – опорно-приводные. Дно тукового ящика образовано одиннадцатью вращающимися тарелками. Каждая тарелка – это круглый диск с бортами, посаженный на ось, к диску прикреплен косозубый венец, находящийся в зацеплении с конической шестерней, закрепленной на валике. Над тарелками расположен вал со сбрасывателями. Над выступающими из ящика тарелками установлен щиток, предохраняющий их от попадания влаги и от сдувания удобрений ветром. Также он способствует равномерному рассеву удобрений. Чтобы в ящике удобрения не застревали, его передняя стенка наклонена под углом 25°. Над тарелками удобрениям не дают образовывать свода два колеблющихся ворошителя, выполненных в виде штанги, к которой приварены две группы пальцев. Пальцы одной группы расположены параллельно передней стенке, пальцы другой группы – параллельно дну ящика. Ворошители колеблются с частотой 9 колебаний в минуту амплитудой 5 см. Для предотвращения поломок ворошителей при попадании в ящик для удобрений твердых предметов в механизме привода смонтирована предохранительная муфта, которая прекращает передачу движения при возрастании крутящего момента до 25 Нм. Высевающие тарелки приводятся в действие от оси левого заднего колеса. Рабочий захват прицепной сеялки 4,2 м.
При движении машины удобрения из тукового ящика через сделанные в дне его вырезы поступают на вращающиеся тарелки. Тарелки выносят удобрения к сбрасывателям, над каждой тарелкой их установлено по два. Один сбрасывает своими лопастями удобрения с периферии тарелки, второй – остальные удобрения, которые подводятся к нему. Норма высева удобрения регулируется изменением частоты вращения тарелок и зазора между дном тарелки и заслонкой.
Использование туковой навесной сеялки позволяет равномерно распределять удобрение по всей поверхности поля и соблюдать нормы внесения независимо от количества удобрений в ящике и колебаний машины при движении по неровному полю.
Универсальная сеялка
Универсальная сеялка – прицепная машина, которая предназначена для рядового посева семян зерновых, зернобобовых и других культур, семена которых близки по размеру и нормам высева к зерновым.
Рядовая сеялка состоит из ящика для семян и минеральных удобрений, высевающих аппаратов, семяпроводов, сошников, механизмов передачи движения и управления. Рама сеялки опирается на два пневматических колеса, третья точка опоры – серьга трактора. На раме монтируются все узлы и механизмы сеялки. Ящики для семян изготавливаются из листовой стали, они чаще имеют два отделения (для семян и гранулированных минеральных удобрений). Каждое отделение закрывается двумя крышками с поручнями, запорными защелками и защелками для фиксирования их в открытом положении. В дне переднего отделения ящика есть отверстия, сквозь которые семена попадают в высевающие аппараты, прикрепленные ко дну ящика. На задней стенке ящика стоят высевающие аппараты для удобрений. Есть возможность использования всего объема ящика только для семян, для этого закрывают окна туковысевающих аппаратов, снимают заслонки, перегораживающие ящик на два отделения.
Катушечный высевающий аппарат состоит из корпуса, желобчатой катушки, жестко посаженной на вал, рядом помещена муфта. Перемещение по оси катушки с муфтой относительно вала ограничивается шплинтами. С валом катушка передвигается в осевом направлении до полного выдвижения в корпус. Перемещением вала изменяется рабочая длина катушки, что влияет на количество высеваемых семян. Вал с катушкой перемещают по сектору рычагом, который фиксируется болтом. Корпус ко дну семенного ящика прикрепляется под отверстием для выхода зерна. В одно боковое отверстие вставляется розетка, а в другое входит муфта. Желобчатая часть катушки из корпуса выдвигается через прорези розетки, которая имеет специальные выступы. Это позволяет высевать мелкие семена небольшими порциями. Дно корпуса выполнено в виде клапана со вставкой и пружиной. Все клапаны корпусов монтируются на общем валике, который рычагом можно поворачивать, изменяя зазоры между клапанами и катушкой на выходе семян, что дает возможность высевать разные по размеру семена. Этим же рычагом высевающие аппараты освобождаются от остатков семян. Туковысевающий аппарат представляет собой катушку с двумя рядами штифтов, расположенных в шахматном порядке (катушечно-штифтовой аппарат). Катушка помещается между стенками корпуса, крепящегося к задней стенке ящика для семян и удобрений. Она не перемещается в осевом направлении с квадратным валом, на который насаживается, и норма высева удобрений регулируется изменением ее частоты вращения. В корпусе есть клапаны, сидящие на общем валике, который можно рычагом поворачивать по сектору. Рычагом все аппараты сразу опорожняют от удобрений. При вращении катушечноштифтовых аппаратов гранулированные удобрения по лоткам поступают в воронки гофрированных семяпроводов. Но они могут быть и гладкими резиновыми, и металлическими. Гладкие резиновые семяпроводы при изменении температуры и влажности быстро выходят из строя. А гофрированные надежнее в работе. В верхней части такого семяпровода укрепляется мундштук для присоединения к аппарату, в нижней – скоба, с помощью которой семяпровод присоединяется к сошнику. Металлические семяпроводы могут быть воронкообразными или спирально-ленточными. Воронкообразные семяпроводы состоят из стальных воронок, соединенных между собой цепочками. Спиральный ленточный семяпровод – это спирально скрученная стальная лента. Присоединяется он так же, как и остальные. Сошники могут быть дисковыми и наральниковыми. Они расставляются в два ряда в 15 см один от другого по ширине сеялки. Поводками они соединяются с сошниковым брусом и штангами с вилками квадратного вала подъема. Окончательную заделку семян выполняют установленные за сошниками подпружиненные зубья-загортачи, которые обоймами крепятся к левому и правому валам. Загортач изготавливается из стальной ленты, конец которой загнут в виде зуба. С плоской частью зуба соприкасается подпружинник, который удерживается хомутиком. Квадратный вал входит в рычаги, шарнирно соединенные со штангой, которая связана с передним круглым валом подъема сошников. При подъеме сошников штангой поворачивается вал загортачей. Валы высевающих аппаратов приводятся в действие от опорно-приводных колес машин через систему зубчатоцепных передач. В транспортное и рабочее положение сошники приводятся гидроцилиндром, включенным в гидросистему трактора. К заднему брусу рамы сеялки кронштейнами крепится подножная доска с поручнем для рабочего, обслуживающего сеялку.
Узкорядная сеялка СЗУ-3,6 отличается от базовой СЗ-3,6 конструкцией двухдисковых сошников. Каждый сошник подает семена в две бороздки, находящиеся на расстоянии 6,5 см.
Зернотравяная сеялка СЗТ-3,6. Ящик для семян и удобрений отличается от ящика базовой сеялки тем, что в отделении для семян установлены ворошилки и нагнетатель для предотвращения образования сводов и обеспечения нормальной подачи семян к высевающим аппаратам.
Прессовая сеялка СЗП-3,6 одновременно с посевом и внесением минеральных удобрений осуществляет прикатывание почвы в рядках. Ее рама впереди опирается на передок с двумя пневматическими колесами, сзади – на четыре секции перекатывающих катков. Заделка семян и удобрений производится естественной осыпью почвы со стенок бороздки, образованной сошниками. Идущие следом катки уплотняют почву. Сеялка может быть переоборудована для работы без прикатывания путем монтирования опорно-приводных колес вместо катков.
Сеялка луговых трав СЛТ-3,6 имеет такое же устройство, как и СЗТ-3,6, но может быть использована для разбросного посева многолетних бобовых и злаковых трав и их смесей. Для этого все сошники и нажимные штанги снимают, на поводках сошников и специальных удлиняющих планках монтируют рассевные воронки, в них закрепляют нижние концы семяпроводов. При движении сеялки семена и удобрения из семенного ящика поступают в воронки, рассеиваются по поверхности поля. Заделываются цепными загортачами.
Зерновые стерневые сеялки СЗС-2,1 и СЗС-9 используются для посева семян зерновых на почвах, которые подвержены ветровой эрозии. Рама устанавливается спереди на самоустанавливающееся колесо, сзади – на прикатывающие катки.
Специальные сошники, выполненные со стрельчатыми лапами, предназначены для предпосевного рыхления почвы. Стерню они оставляют на поверхности поля, семена и удобрения укладывают на ровное ложе бороздки.
Во время движения сеялки с включенными в работу сошниками семена из переднего отделения ящика и удобрения из заднего подаются высевающими аппаратами в воронки семяпроводов, по ним самотеком поступают в раструбы сошников и по направителям – на дно открытых сошниками бороздок.
От работы сошников зависит качество заделки семян. Щеки сошника поддерживают открытые стенки бороздки в верхней части.Окончательная заделка семян осуществляется загортачами, которые установлены за сошниками.
Раздел 4. Дорожно-строительная техника
Автовышка
Автовышка – самоходное транспортно-подъемное средство, используется в строительных, дорожных работах для подъема рабочих, инструмента и материалов, при ремонте зданий и сооружений, окраски, очистки, облицовки, штукатурки. Основное рабочее устройство – подъемная вышка на базе автомобиля, имеющая привод от двигателя автомобиля через коробку отбора мощности. Производство таких автовышек развивается с середины XX в. с ростом автомобильной промышленности и потребностей различных отраслей производства, так как они имеют очень широкое применение. Самая распространенная конструкция – это телескопический подъемник-вышка, с люлькой или рабочей площадкой. Модификации в основном зависят от высоты подъема люльки или площадки и различаются от 6—23 м, а иногда и более. Водитель из кабины автомобиля управляет работой, осуществляя подъем, спуск, вышки повороты люльки и рабочей площадки. На самой рабочей площадке также имеется устройство для управления ее поворотами. Во время работы для устойчивости автовышки устанавливают по обеим сторонам автомобиля опоры-аутригеры. Дальнейшее усовершенствование конструкции такой автовышки направлено на увеличение высоты подъема, грузоподъемности, маневренности, надежности управления и эксплуатации.
Автогрейдер
Автогрейдер – самоходное колесное средство – автомобиль предназначается для разравнивания грунта и дорожностроительных материалов, таких как гравий, щебень, песок, для профилирования насыпей, перемещения грунта или песка, используется при строительстве и ремонте автомобильных и усовершенствованных дорог и покрытий, строительстве каналов. На автомобильном серийном шасси установлено основное рабочее устройство – полноповоротный отваг криволинейного профиля. Дополнительное сменное оборудование бульдозера или снегоочистителя. Управление автогрейдером осуществляет водитель из кабины при помощи механического или гидравлического привода. Сам грейдер – это отвал, перемещающий, разравнивающий грунт, отвал с ножом смонтирован на раме, он способен подниматься, опускаться, поворачиваться. Длина ножей 2,5—4,5 м. Современные автогрейдеры появились в XX в. с развитием автомобильной промышленности и ростом потребности различных отраслей народного хозяйства. Модификации различаются по конструкции и размеру основного устройства – отвала, который зависит от назначения. Дальнейшее совершенствование конструкции таких автомобилей направлено на увеличение производительности, маневренности, использования различных дополнительных устройств, расширение их использования.
Автогудронатор
Автогудронатор – самоходное колесное средство – автомобиль, используется в строительстве и ремонте дорожного покрытия для равномерного распределения по обрабатываемой поверхности органических материалов на основе гидронабутума и дегтя. На серийном шасси автомобиля установлены рабочие устройства автогудронатора: цистерна емкостью 7000 л, для материала – гудрона, система подогрева материала до 180 °С, состоящая из горелок и топливного бака, насос – для распределения материала по поверхности.
Дополнительные устройства: контрольно-измерительные приборы, манометр, технометр, указатель уровня материала в цистерне. Работой автогудронатора управляет водитель из кабины, привод насоса от двигателя автомобиля через коробку отбора мощности.
Автогудронатор набирает материал и транспортирует его к месту распределения по покрытию дороги.
Такие современные автомобили – гудронаторы появились в XX в. с развитием машиностроения и ростом потребности производства. Модификации различаются по емкости и производительности. В основном широкое распространение имеют автомобили-гудронаторы, но также используются и прицепные гудронаторы – перекачивающие и распределяющие устройства, работающие вместе с автобитумовозом – автомобилем-цистерной, емкостью до 15 м2, для транспортировки битумов. Цистерна имеет цилиндрическую форму и сделана из стали или алюминиевых сплавов.
Автопогрузчик
Автопогрузчик – самоходная транспортно-подъемная машина, для погрузки и разгрузки строительных материалов в таре штучных грузов, на строительных площадках при различных ремонтных работах. Основное рабочее устройство такого автопогрузчика – вилочный захват, который перемещается вдоль вертикальной телескопической рамы при помощи гидроцилиндра, расположенного внутри этой рамы. Конструкция рамы позволяет ей отклоняться вперед и назад на 15° для придания грузу, находящемуся на вилах, устойчивости, при его перевозке и для удобства разгрузки. Когда автопогрузчик движется с взятым на вилы грузом, то рама отклоняется к кабине, что придает грузу устойчивость при выгрузке, рама отклоняется и это облегчает разгрузку, так как такие автопогрузчики используются для тяжеловесных грузов – ящиков со стройматериалами, блоков. Управляется автопогрузчик рычагами гидравлической системы с места водителя из кабины. Такие автопогрузчики в различных отраслях производства распространены с XX в., что связано с ростом машиностроения и потребностями народного хозяйства. Модификации в основном различаются по грузоподъемности 3, 5 т и наличии различных сменных рабочих приспособлений, таких как ковш, стрела, захваты. Дальнейшее совершенствование конструкции идет по увеличению грузоподъемности, маневренности, усовершенствованию систем управления.
Авторемонтная машина
Авторемонтная машина – самоходное транспортное средство – автомобиль-мастерская. Используется для ремонта и технического обслуживания автомобилей, работающих на строительстве и ремонте дорог, вдалеке от специализированных ремонтных баз. Такая авторемонтная машина – это кузов-фургон на базе шасси грузового автомобиля повышенной проходимости. Кузов – легкий, его назначение – обеспечить защиту находящихся в нем инструментов и выезжающей к месту ремонта рабочей бригады. Рабочее оборудование авторемонтной машины – это различные приборы и ремонтные инструменты, автономная электростанция, передвижные грузоподъемные средства.
Автосамосвал
Автосамосвал – самоходное мощное транспортное средство для перевозки грузов большой массы – грузовой автомобиль или прицеп. На базе серийного автомобильного шасси установлен кузов. Двигатель дизельный. Кузова различаются по способу разгрузки. Основной вид – самоопрокидывающийся кузов бункерного типа, для опрокидывания которого служат гидравлические подъемники телескопического типа, работой которых управляет водитель из кабины. Такие самоопрокидывающиеся кузова имеют наибольшее распространение, но также используются и кузова с принудительной шнековой разгрузкой. Такие большегрузные самосвалы появились в середине XX в. с ростом автомобильной промышленности и потребностями различных отраслей производства, так как предназначены они для работы на строительстве дорог, плотин, в карьерах, в районах низкой проходимости. Изготавливаются они из высокопрочных сталей или сплавов. Модификации различаются по назначению и по грузоподъемности 3—10 т, 27—40 т и более, это карьерные большегрузы. Дальнейшее совершенствование направлено на увеличение грузоподъемности, проходимости, скорости, на использование новых технологий и систем управления.
Асфальтобетоноукладчик
Асфальтобетоноукладчик – cамоходная машина, используется для укладки и распределения асфальтобетона при строительстве дорожных покрытий. Ходовое устройство гусеничное или колесное. Машины различают по типам, в зависимости от производительности: тяжелого типа 100 т/ч и легкого типа 50 т/ч. Асфальтобетоноукладчики тяжелого типа используют при строительстве дорожных объектов с большим объемом работ. Асфальтобетоноукладчики легкого типа применяют при вспомогательных небольших объемах работ. Принцип работы асфальтобетоноукладчика состоит в том, что асфальтобетонная смесь из самосвала поступает в бункер укладчика и подается скребковыми питателями к шнекам, которые распределяют ее по ширине укладываемой полосы. Укладчик оснащен также трамбующим брусом и выглаживающей плитой. Трамбующий брус выполняет разравнивание и уплотнение асфальтобетонной смеси, выглаживающая плита осуществляет отделку поверхности дорожного покрытия. Выглаживающая плита имеет специальное устройство для обогрева, предотвращающее прилипание смеси.
Асфальтоукладчик.
Асфальтобетон – строительный материал из уплотненной смеси щебня, песка, битума, горячий асфальтобетон укладывается при 120 °С, теплый – до 80 °С. Холодный не ниже 10 °С. Готовится асфальтобетон в специальной установке – асфальтобетоносмесителе. Устройство установки включает барабан для сушки и нагрева щебня и песка, смеситель, в котором песок и щебень сортируются и дозируются и после смешиваются с битумом. Смесители бывают с вертикальным или горизонтальным движением материалов. Перемешивание осуществляют мешалки периодического и непрерывного действия.
После просушки и нагрева в барабане песок и щебень подаются ковшовым элеватором в сортировочное устройство и в соответствующие отсеки бункера. Негабаритный материал отводится по лотку.
Каждая группа материалов взвешивается на весовом устройстве и после поступает в двухвальную лопастную мешалку, из устройства дозирования в нее подается насосом битум, смесь перемешивается до готовности и поступает в транспортное средство. Асфальтобетонная смесь должна соответствовать плотности, влагоустойчивости, прочности, что зависит от нагрузок и климатических условий. Все материалы смеси стандартизированы.
Бетононасос
Бетононасос – машина, предназначенная для перемещения бетонной смеси по бетоноводу на место ее укладки. Бетононасосы различаются по конструкции и по роду привода. Конструкция одно– или двухцилиндровая. Привод – кривошипно-шатунный или гидравлический. В обеих конструкциях поршень из бункера насоса засасывает бетонную смесь, при этом нагнетательный клапан закрыт, а всасывающий открыт. Обратным движением поршень выталкивает смесь в бетоновод. Длина хода поршня в рабочем цилиндре и постоянная скорость у бетононасоса с гидравлическим приводом больше, чем у кривошипношатунного. Это дает равномерное движение бетонной смеси и снижение сопротивления ее движению в бетоноводе. Бетононасосы подают смесь по вертикали – 40 м и по горизонтали до 300 м. Бетоновод состоит из отдельных труб с быстроразъемными соединениями. Производительность насосов 5—40 м3/ч.
Бетоносмеситель
Бетоносмеситель – машина, приготавливающая бетонную смесь способом перемешивания ее составляющих компонентов: вяжущего, заполнителей воды. Основное рабочее устройство бетоносмесителя – смесительный барабан, приводимый во вращение электродвигателем. Прототип бетона применяли в строительстве еще в Древнем Риме, и в качестве вяжущих веществ, компонентов использовали известь, гипс, глину. В XVIII в. производство бетона возобновилось в странах Европы, в это время стали использовать цемент в составе бетона. Первый цементный завод был построен в 1840 г. во Франции, в 1855 г. в Германии, в 1871 г. в США. Современные бетонные смеси приготавливаются на заводах или в передвижных бетоносмесителях. Заводы оборудованы стационарными смесителями. Для работ на строительных площадках используют передвижные бетоносмесители или автобетоносмесители – они имеют кузов или бункер, смонтированный на шасси грузового автомобиля. Объем готового замеса составляет более 1600 л. Характер работы бетоносмесителей различный: цикличного действия – выдающие готовую смесь порциями, и непрерывного действия – непрерывно перемешивающие компоненты и выдающие готовую смесь. Самый распространенный способ приготовления смеси – гравитационный: бетонная смесь перемешивается лопастями, укрепленными на внутренней поверхности во вращающемся барабане. Другой способ – принудительное перемешивание лопастями, передвигающимися в неподвижном барабане. Автобетоносмеситель перемешивает бетонную смесь во время своего движения к месту укладки бетона на строительном объекте.
Бетоноукладчик
Бетоноукладчик – машина, осуществляющая прием и распределение бетонной смеси на заданном рабочем участке при выполнении строительных работ. Бетоноукладчики различаются по назначению: для строительства бетонных покрытий дорог, площадок, фундаментов, полов и для изготовления железобетонных изделий. В строительстве дорог применяются бетоноукладчики на рельсовом ходу. На строительных площадках – самоходные бетоноукладчики на гусеничном ходу, они оборудованы устройством, принимающим бетонную смесь из бетоновоза или автобетоносмесителя. Подачу и распределение бетонной смеси осуществляет поворотный ленточный транспортер. Специальные устройства разравнивают бетонную смесь, уплотняют и заглаживают.
Битумовоз
Битумовоз – транспортное средство, предназначенное для перевозки битумов и жидких битумных материалов, имеющих температуру до 200 °С. Это специализированный грузовой автомобиль, или прицеп, полуприцеп. Резервуар для битума – горизонтальная цистерна емкостью до 15—25 м3. Битумовозы имеют специальные подогревательные устройства на дизельном топливе или керосине, чтобы обеспечить постоянную заданную температуру во время транспортировки. Битумовозы также оборудованы термометрами, указателями уровня налива, металлическими рукавами для слива жидкого битума. Битомовоз также может использоваться как автогудронатор, при строительстве дорог, если на него установить распределитель. Битумы – это природные образования – нефть, нефтепродукты, и искусственные, получаемые от переработки природных – каменноугольной, сланцевой – смол. Битумы использовались в 3000 г. до н. э. для покрытия водохранилищ, зернохранилищ, в строительстве тоннелей и зданий. Сейчас битумы имеют очень широкое применение в различных областях строительства и производства. На их основе изготавливают битумные лаки, пластики, изоляционные материалы кровельные. Битумы из твердых топлив – торфа и бурого угля получают растворителями и используют в литейной и электротехнической промышленности.
Бульдозер
Бульдозер – самоходная машина, предназначенная для землеройных работ – трактор или тягач, на гусеничном или колесном ходу. Основное рабочее устройство – навесной криволинейный отвал, щит, находящийся вне ходовой части машины. Бульдозер выполняет послойное копание, перемещение грунтов, полезных ископаемых, дорожностроительных материалов – песка, гравия, щебня, планирует дорожное покрытие, используется в дорожном строительстве, в постройке каналов, дорог и других объектов. Бульдозеры различаются по типу отвала: неповоротный, поворотный, универсальный. Неповоротный отвал установлен перпендикулярно продольности оси машины. Поворотный отвал, устанавливаемый под углом от продольной оси машины или также перпендикулярно. Универсальный отвал – состоит из двух шарнирно-сочлененных половин, которые можно устанавливать под любыми углами, к продольной оси машины или перпендикулярно к ней. Все отвалы имеют привод – гидравлический, канатный, электромеханический и выполняют движения – подъем, опускание, поворот, наклон отвала. Современные бульдозеры появились в середине XX в. на производствах тракторостроения. Они сконструированы на базе трактора, оснащены навесными рабочими устройствами различных конструкций, сменным оборудованием: откосниками, открылками, рыхлительными зубьями, уширителями, предназначенными для землеройных или планировочных работ. Основные характеристики бульдозера – тяговые качества, производительность, металлоемкость. Силовая установка бульдозера включает двигатель, силовую передачу, сцепление, коробку передач, соединительную муфту, центральную и конечную передачу. Ходовая система гусеничного бульдозера включает подвеску, гусеничные цепи, колеса – направляющие и ведущие, поддерживающие ролики, опорные катки. Ходовая система колесного бульдозера включает подвеску, оси, колеса с пневматическими шинами – направляющие и ведущие, механизмы управления – это рулевое устройство и тормоза. Электрическое оборудование – это источник электрического тока – аккумуляторная батарея, генератор, устройства освещения, вентиляции, звуковой и световой сигнализации. Работой бульдозера управляет водитель из кабины.
Виброкаток
Виброкаток – дорожная машина для уплотнения грунтов или дорожных покрытий, в несколько раз эффективнее использования статического катка. Основное рабочее устройство виброкатка – вальцы, одни из которых совершают вибрационные, колебательные движения. По способу перемещения виброкатка различаются – прицепные и самоходные. Прицепные виброкатки – одно– и двухсекционные, имеют гладкие, решетчатые вальцы или с шипами. Самоходные виброкатки имеют гладкие вальцы. Наибольшее распространение имеют прицепные односекционные виброкатки. Привод центробежного вибровозбудителя от двигателя внутреннего сгорания, а также самоходные с двумя вальцами и с механическим приводом вибровозбудителя и катка. Современные дорожные машины-катки появились в XX в., с общим развитием машиностроения. Усовершенствование их конструкции направлено на увеличение производительности.
Виброплита
Виброплита – вибрационная машина, используется в дорожно-строительных и ремонтных работах для уплотнения грунтов или дорожных оснований из гравия, щебня. Виброплиты имеют различие по способу перемещения, по виду привода. По способу перемещения бывают виброплиты ручные, прицепные, навесные, самопередвигающиеся, переставляемые. По виду привода виброплиты бывают: электрические, пневматические, гидравлические, с двигателем внутреннего сгорания. Более распространены виброплиты самопередвигающиеся с приводом от двигателя внутреннего сгорания. Виброплита передвигается за счет горизонтальной составляющей возмущающей силы. Конструкция виброплиты включает: основное рабочее устройство – плиту, вибровозбудитель направленного действия, прижимные амортизаторы, управление, двигатель внутреннего сгорания. Принцип работы виброплиты основан на сообщении плите колебательного вибрационного движения, интенсифицирующего рабочий процесс. Совершенствование конструкции виброплиты направлено на увеличение производительности и разработку систем защиты от вредного действия вибрации.
Виброплощадка
Виброплощадка – вибрационная машина для уплотнения бетонной смеси при изготовлении бетонных конструкций и изделий в строительных работах. Виброплощадки различаются по характеру колебаний: круговые, вертикальные, горизонтальные. По конструкции виброплощадки бывают рамного и блочного типа. Виброплощадка состоит из виброблоков, прижимов, опорных пружин, карданных валов, электродвигателя. Принцип работы виброплощадки основан на передаче колебаний от нее закрепленной на ней форме с бетонной смесью с помощью прижимов. Прижимы бывают пневматические, механические или электромагнитные.
Грейдер-элеватор
Грейдер-элеватор – землеройная машина, оснащение автогрейдера, или также бывают самоходные прицепные модификации. Производительность 500—1600 м3/г и более, основан на непрерывном действии – срезании грунта и перемещении его в отвал или в транспортное средство. Нож грейдера, имеющий вид диска 600—1000 мм в диаметре, срезает грунт, который направляется по наклонному ленточному конвейеру длиной 8—10 м. Такие устройства используются при строительстве дорог, каналов, насыпей, в планировочных работах.
Землечерпальная машина (снаряд)
Землеройная плавучая машина используется для копания и извлечения грунта из воды, при дноуглубительных работах, строительстве подводных котлованов. Первые землечерпальные машины использовались для добычи полезных ископаемых, они назывались «дрога». И появились в конце XIX в.: в 1870 г. в Новой Зеландии и в 1893 г. в России, на Амуре, в 1900 г. на Урале.
Современные землечерпальные машины различают по типам в зависимости от рабочего оборудования: одночерпаковый штанговый, многочерпаковый, грейферный.
Одночерпаковая штанговая машина – это плавучий экскаватор с черпаком емкостью 12 м3, перемещается с помощью подъемных свай, используется для выработки тяжелых каменистых грунтов, имеет скалодробильное устройство.
Многочерпаковая машина непрерывного действия. Принцип ее работы основан на извлечении грунта черпаками, соединенными в замкнутую цепь, охватывающую два барабана, верхний барабан имеет привод. Емкость черпака до 1,5 м3. Перемещается машина с помощью судовых лебедок. Грунт перемещается насосами, шлангами или конвейерами. Используется для разработки тяжелого или легкого грунта.
Грейферная машина имеет поворотный грейферный кран, иногда несколько, до четырех. Грейферы бывают 2– или 4-створчатые, емкостью до 4 м3, что зависит от грунта, который перевозится в трюме машины. Такие грейферные машины используются для дноуглубительных работ около берега и передвигаются на тросах при помощи судовых лебедок.
Драга
Драга – плавучая землечерпальная и горно-обогатительная машина с комплексом оборудования для добычи полезных ископаемых из-под воды. Драги используют для разработки прибрежных россыпей или водоемов. По назначению драги различают на 2 класса: континентальные и морские.
Континентальные драги используют в замкнутом водоеме, они смонтированы на плоскодонном судне.
Морские драги используют в прибрежной зоне и даже в глубоководной части морей или океанов. Они смонтированы на килевых судах, самоходных или буксирных, и приспособлены к работе в открытом море при штормовом волнении. Драга имеет промывочнообогатительное оборудование, находящееся на самом судне или на отдельной плавающей установке.
И континентальные, и морские драги различаются по роду энергии, по способу передвижения, по глубине разработки, по принципу работы, по емкости черпаков.
Род энергии: электрический, паровой, дизельный. Способ передвижения: канатно-свайные, канатно-якорные. Глубина разработки: от 6 м и более 50 м. Принцип работы: одночерпаковые, многочерпаковые, грейферные.
Емкости черпаков: малые до 100 л, средние до 250 л, большие до 600 л.
Самая мощная в мире драга построена в России в 1969 г. на Иркутском заводе тяжелого машиностроения. Емкость ее черпаков 600 л, глубина копания до 50 м. Дальнейшее развитие землечерпальных машин направлено на оснащение их высокопроизводительным оборудованием, системами автоматизированного управления, контроля, на использование электронных устройств, повышение эффективности.
Измельчительные устройства
Измельчительные устройства – устройства, предназначенные для тонкого дробления твердого металла. Используются в горно-обогатительной, химической, металлургической, строительной промышленности. Принцип действия измельчения основан на деформации материала при воздействии на него определенными приспособлениями и определенными способами. Процесс измельчения материала был известен в древности. Самыми первыми простейшими измельчительными устройствами были каменные ступка и пест. Ими пользовались люди за 8000 лет до н. э., жернова с ручным приводом появились за 3500 лет до н. э. в Китае и Египте. Но, как правило, они использовались для измельчения зерна, частично при добыче полезных ископаемых и в строительстве. И еще очень долго процесс измельчения оставался ручным и низкопроизводительным. И только в XIX в. появилось машинное измельчение с общим развитием машинного производства.
Самое первое машинное устройство для измельчения (шаровая мельница) появилось во второй половине XIX в. Современные измельчительные устройства-мельницы различаются по назначению и конструкции. Они бывают барабанные, роликовые, кольцевые, вибрационные, струйные, бегуны. Барабанные мельницы (шаровые, стержневые) используются для измельчения твердых материалов в химической, цементной промышленности, при добыче полезных ископаемых.
Роликовые и кольцевые мельницы используются для измельчения средних и мягких материалов (фосфоритов, угля). Вибрационные и струйные мельницы используются для тонкого и сверхтонкого измельчения малых частиц.
Бегуны используют для измельчения кварца, шпата, глины в строительной промышленности. Производительность измельчительной машины зависит от материала. На расходуемую для измельчения энергию влияют прочность и размеры материала, степень загрузки измельчительного устройства. Чтобы не допустить переизмельчения материала, процесс идет в замкнутом цикле, при разгружении материала из мельницы измельченный продукт заданных фракций отводится, но недостаточно измельченный возвращается обратно. Чтобы добиться тонкого измельчения, процесс осуществляют в две-три стадии, используя две-три мельницы, иногда работающие в разных циклах – одна в открытом, другая – в замкнутом цикле. Дальнейшее усовершенствование конструкции измельчительных машин направлено прежде всего на повышение производительности.
Кабелеукладчик
Кабелеукладчик – устройство для прокладки кабелей. Кабелеукладчики различаются по конструкции, которая зависит от назначения. Основное рабочее устройство – приспособление, прокладывающее кабель. По конструкции кабелеукладчики бывают: ножевые, гидравлические, роторные.
Ножевой кабелеукладчик состоит из рабочего расклинивающего ножа и переднего ножа, барабанов, на которых намотан кабель, кассеты, роликов, уменьшающих трение кабеля внутри кассеты. Ножевой кабелеукладчик во время работы буксируется тракторами. При движении рабочий нож расклинивает грунт, образует узкую щель между поверхностью грунта и своей расклинивающей частью, глубина щели достигает 1,5 м. К тыльной стороне ножа на шарнирах прикреплена пустая кассета, через которую пропускается кабель (или сразу несколько кабелей) и укладывается на дно щели. Передний нож предназначен для разрыхления верхнего слоя грунта и устранения препятствий. Тяговое усилие зависит от плотности грунта, глубины прокладки и достигает до 500 км, такое усилие дает совместная работа 3 тракторов, но иногда их может быть и семь. Производительность ножевого кабелеукладчика 5 км трассы в день. С помощью ножевого кабелеукладчика прокладывают кабель в глинистых, песчаных, каменистых грунтах, талых, мерзлых, но после их предварительного разрыхления. Также его используют для прокладки кабеля через водоемы – реки, каналы. Если по водоему тракторы не могут пройти, при глубине более 1 м, то тяговое усилие передается при помощи длинных тросов, от идущих по берегу тракторов.
Подводный ножевой кабелеукладчик предназначен для заглубления кабеля в дно, прибрежных участков, чтобы защитить кабель от повреждения тралами. Подводный кабелеукладчик буксирует судно, которое движется со скоростью до 3 км/ч. Кабелеукладчик при этом движется по дну на глубине до 200 м на специальных полозьях и его нож роет траншею до 0,1 м шириной и глубиной до 0,7 м. Такой подводный кабелеукладчик оборудован приборами, контролирующими его работу, измеряющими скорость и расстояние и передающими все данные на буксирующее судно по специальному кабелю, соединяющему кабелеукладчик и кабельное судно.
Гидравлический кабелеукладчик используется для прокладки кабеля через реку или море. На кабельном судне находится насос. Он под напором подает воду по трубе, конец трубы находится под водой на заданной глубине, вода выходит из трубы через сопло и образованной сильной струей размывает грунт. Получается траншея, в нее укладывается кабель, проходящий через другую трубу, сматывающийся с барабана, который тоже находится на кабельном судне. Производительность такого способа укладки кабеля до 10 м/ч. Самое первое кабельное судно появилось в 1858 г. в Великобритании, с него был проложен первый телеграфный кабель, соединяющий Великобританию с континентальной Европой. В 1865—1874 гг. были проложены трансатлантические кабели также с английского кабельного судна. В конце XX в. такие кабельные суда есть во многих странах, весь кабельный мировой флот имеет более 30 судов водоизмещением 8000, 12 000, 17 000 т. Кабельное судно устроено так, что в его трюмах находятся баки цилиндрической формы, в которых уложено витками несколько тысяч километров кабеля. На палубе находятся специальные ангары, в которых закреплены усилители электрических сигналов. Концы кабеля присоединяют к усилителю. На корме судна и на носу с обоих бортов находятся кабельные машины-лебедки с электроприводом, с усилием до нескольких сотен кН. Кабельная машина оснащена натяжным устройством со шкивами или гусеничным. На носу судна находится кронштейн со шкивами для кабеля. Таким устройством осуществляется прокладка кабеля на глубину до 6000 м, скорость продвижения до 15 км/ч. На кабельном судне есть оборудование, непрерывно контролирующее прокладывание кабеля и имеющее связь с береговой станцией. Также на судне имеются устройства – захваты и поплавки для поиска и подъема кабеля с целью его ремонта. Если кабель прокладывается в прибрежных участках моря или через небольшие реки, каналы, то применяются обычные буксирные и грузовые суда, на которых устанавливаются лебедка и шкивы для прокладки кабеля.
Роторный кабелеукладчик – это самоходный роторный экскаватор с прицепной тележкой, оборудованной устройствами для погрузки, транспортировки и укладки кабеля. Такой кабелеукладчик используется для прокладки кабеля и в талых, и в мерзлых грунтах. Основное рабочее устройство роторного кабелеукладчика – диск с режущими зубьями. Производительность роторного кабелеукладчика до 1 км трассы в день.
Канавокопатель (траншеекопатель)
Канавокопатель – машина для разработки (копания) канав, кюветов, траншей, каналов, используется в строительстве, земляных работах, мелиорации, разработке полезных ископаемых. Машина – это трактор, как правило, на гусеничном ходу с основным рабочим устройством для копания. Различается по типу рабочего устройства: пассивное – плуг или отвал, или комбинированное многоковшовое устройство и шнек, и активное – ротор или фреза. Трактор может быть самоходный или прицепной. Канавокопатель, оборудованный фрезой, используют для строительства осушительных каналов в торфяных болотистых грунтах, глубина канала до 2 м. Фреза вращается со скоростью 30 м/с, создается усилие среза грунта, измельчения торфа и выброс его на расстояние до 20 м. Канавокопатель, оборудованный ротором, применяют при строительстве оросительных каналов в плотных грунтах. Глубина канала до 2 м. Скорость вращения роторов 8 м/с. При этом грунт разбрасывается на небольшое расстояние от канала и применяется для постройки дамб. Фрезерные и роторные канавокопатели прокладывают канал за один или несколько проходов, что зависит от заданной его глубины, ширины и категории грунта. Их производительность до 800 м3/ч. Канавокопатель, оборудованный прицепным или навесным плугом или отвалом, также предназначен для прокладки каналов. Основное рабочее устройство плужного канавокопателя – двухотвальный плуг, который использует тяговое усилие трактора, образует канал до 1,2 м глубиной за один проход. Его производительность 1800 м3/ч. Основное рабочее устройство отвального канавокопателя – два симметричных грейдерных отвала, они разрабатывают грунт послойно, формируют откосы канала и его дно. Производительность отвального канавокопателя до 1500 м3/ч. Комбинированный канавокопатель применяют для прокладки кюветов, при выполнении землеройных работ на железной дороге. За один проход он прокладывает канал до 3 м глубиной. И каждый из его рабочих приспособлений выполняет разработку и отделку определенной части сечения канала. Производительность комбинированного канавокопателя зависит от числа проходов и использованных комбинированных рабочих устройств. Канавокопатели имеют широкое применение в различных отраслях производства.
Каток
Каток – машина, относящаяся к типу дорожных машин, используется в строительных, дорожных работах для уплотнения грунтов, покрытий, дорожных оснований способом укатывания. Катки различаются по способу перемещения и по принципу действия. По способу перемещения катки бывают самоходные и прицепные. По принципу действия – статические и вибрационные. Основное рабочее устройство катков – стальные вальцы – гладкие, решетчатые или имеющие на своей поверхности шипы. В некоторых конструкциях катков вместо жестких вальцов используются пневматические шины. Эффективность уплотнения зависит от массы катка, для ее увеличения применяют нагружение машины балластом (железобетон, песок), масса дорожных катков от 5 до 50 т. Скорость движения 2—8 км/ч. Для уплотнения грунта и дорожных оснований используют прицепные катки с гладкими вальцами или на пневматических шинах. Для уплотнения дорожных покрытий используют самоходные катки с гладкими вальцами статического или вибрационного действия.
Кирковщик
Кирковщик – самоходная колесная машина, используется при ремонте дорожных покрытий. На автомобильном шасси смонтировано основное рабочее устройство – кирковщик, имеющий 7—11 зубьев, которые разрезают дорожное покрытие при ремонте дорог или коммуникаций, управление механическое или гидравлическое, привод от двигателя автомобиля.
Ковш
Ковш – основное навесное устройство многих дорожных машин. Емкость, имеющая литую конструкцию, сварную или штампованную. Ковш предназначен для захвата грунта, строительного материала или горной породы, отделения его, перемещения и разгрузки или погрузки в транспортное средство. Ковш имеет режущую кромку, как правило, с зубьями которой он легко врезается в разрабатываемый пласт. Разгружается ковш со стороны режущей кромки, а также способом открывания дна. Характеристика ковша: прочность, способность к быстрому наполнению и разгрузке. Ковшами разных конструкций оборудованы экскаваторы, землечерпалки, погрузчики. Ковши прикрепляются у одноковшовых погрузчиков на рукоятях или раме, у многоковшовых экскаваторов на рабочих цепях, у грейферов подвешиваются к несущей конструкции. Ковши различаются емкостью, которая зависит от применения. Одноковшовые экскаваторы имеют ковш емкостью 0,15—200 м3, многоковшовые имеют ковши емкостью до 7 м3. Одноковшовые погрузчики имеют ковш емкостью 0,07—30 м3